Working with Castellated Beam
A castellated beam is created by slicing an I-beam longitudinally along
its web in a specific pattern. The goal is to separate and then rejoin the beam
with a deeper web. These beams are categorized based on the shape of the
openings in the web section, with common shapes including hexagonal, circular
(also known as cellular), octagonal, and diamond.
Additionally, castellated beams are useful in situations with height
limitations. The openings in the beam web allow for easy passage of piping.
However, these benefits come with trade-offs. The web openings introduce
additional failure mechanisms, necessitating checks such as Vierendeel,
horizontal shear, vertical shear and web post shear buckling. Furthermore, the
section properties used in finite element analysis differ from those of
conventional solid beams.
To insert a castellated steel beam:
1. Pick the Steel Beam command on the Modeling > Frame ribbon tab.
2. Insert a linear or curved frame member as usual.
3. On the Frame
Properties window, switch to Castellated tab.
4. You can select a Hexagonal or Circular Opening.

The code design
formulations are given for circular (cellular) and hexagonal openings, thus rectangular openings are not supported.
5. Place the openings
by specifying their Count or clear Spacing. You can also specify Start
Offset and End Offset.
6. Also specify the
dimensions of the web openings using the Width, Height or Diameter fields.

Important:
While inserting the castellated steel
frame member, choose a hot-rolled profile or built-up profile that will
have the final profile depth.
If the final profile will have 460 mm
depth after slicing and welding, then choose, for example, a W18x46 hot-rolled
profile, instead of the original profile before the cut.
7. You may want to infill
some of the openings, in this case specify the number of openings to be infilled
in respective order. For example, if you want to infill second, third and fifth
opening you can enter 2, 3, 5 in the Closed Holes field. This
does not have any effect on analysis or design. It can be used for detailing
purposes.

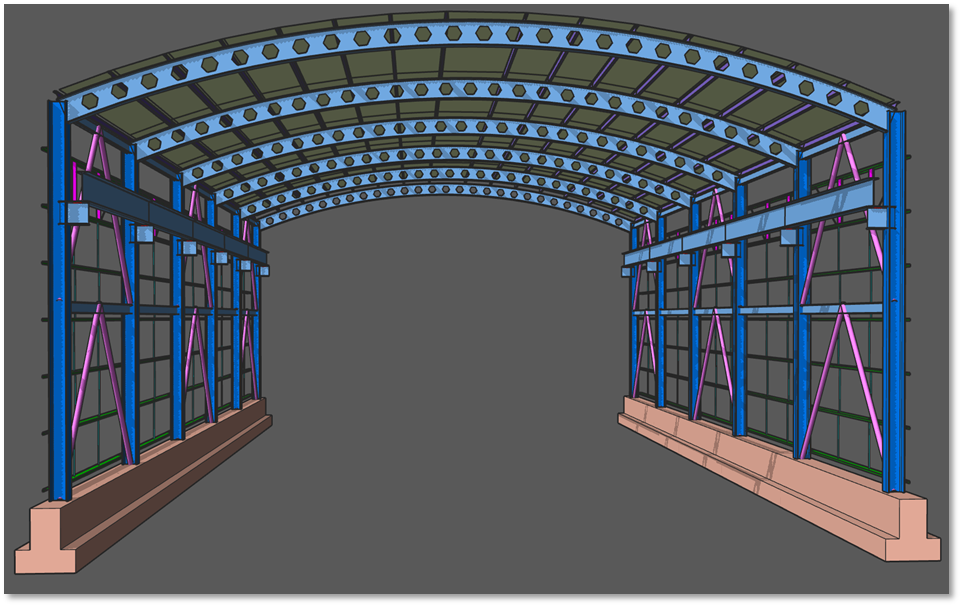
Due to the presence of the significant number of web openings, castellated
and cellular beams cannot be treated as solid-web members or members with web
openings. These structural members are highly indeterminate elements, which do
not lend themselves to a simple method of analysis. The following limit states
should be investigated when designing castellated or cellular beams:
- Compactness and local buckling
- Overall beam flexural strength
- Vierendeel bending of tees
- Web post buckling
- Axial tension/compression
- Horizontal shear
- Vertical shear
- Lateral-torsional buckling
The first step in designing both castellated and cellular beams is to
calculate the overall bending moment and shear force at each opening and web
post caused by external loads. These forces will be referred to as global
forces. The global forces will be used to compute localized forces in the top
and bottom tees, the web posts, and the gross section. The components (tees and
web posts) of the beams will then be examined for failure under the localized
forces.

Important
ProtaStructure 2026 performs castellated beam checks according to Eurocode 3, AISC360
and Turkish Steel Design Code.
ProtaStructure
currently supports only the non-composite castellated beams.
[Reference: AISC Design Guide 31 – Castellated and
Cellular Beam Design]
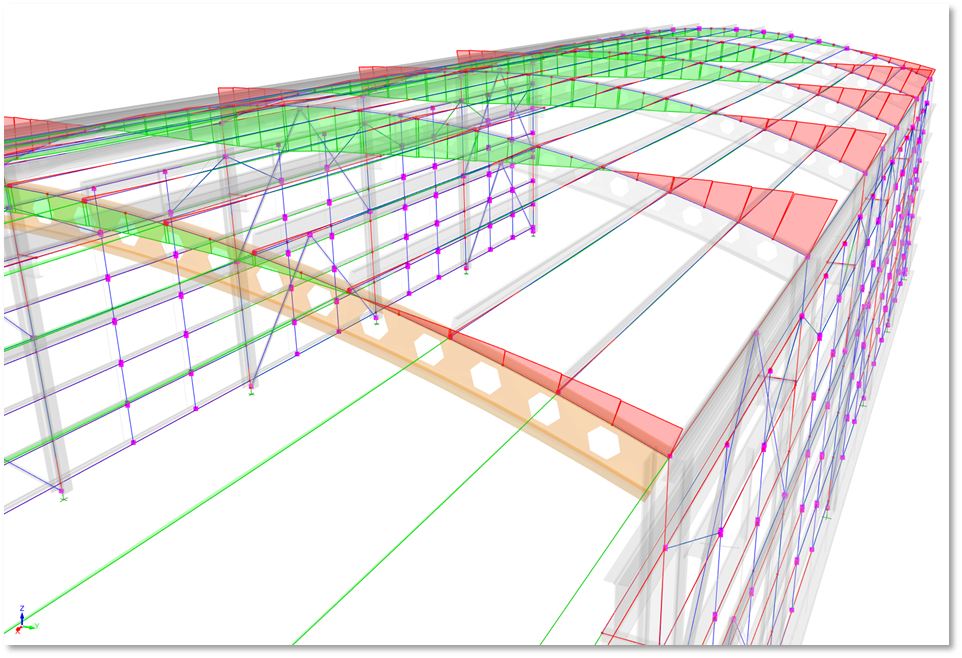
Analysis results shown for a model including castellated non-composite castellated beams
Castellated Steel Beam Design UI and Detailed Report in ProtaStructure
The web openings are automatically communicated to ProtaSteel for
detailing. Openings are defined by cut object, so you can modify them easily if
needed.
Related Articles
Castellated Beams
A castellated beam is created by slicing an I-beam longitudinally along its web in a specific pattern. The goal here is to separate and rejoin the beam with a deeper web. Castellated beams offer increased depth compared to the original section, while ...
Steel Design & Composite Member Settings
Steel design & composite member setting is important to preset before starting to design any steel or composite steel members. By presetting these design parameters can save a significant amount of time for user compare to user who set after ...
Working with Steel Frame
The “Frame Member” option enables users to model steel beams, composite beams, girts, purlins, braces and frame groups (to model multiple frames). This allows users flexibility to model steel structures anywhere in the model. Frame member sections ...
Composite Beam Design General Principles
ProtaStructure supports a powerful composite slab/beam design. The overview of the composite slab modeling, analysis, and design is as follows: 1. Metal decks can be chosen from a Metal Deck Library. 2. Shear studs can be specified from a Stud ...
Working with Steel Truss
Auto-generated steel trusses of any shape (e.g. Pratt, Warren, mono-pitched, duo-pitched truss). The trusses can be easily moved and copied to another location. Defining a New Truss Before inserting a truss, there must have supports created for ...