The beam forces that are automatically designed for in the beam section design are Major Bending Moment, Major Shear Force & Torsion.
The beam forces that are not automatically designed for (or even checked) are Axial Tension Force, Minor Axis Bending Moment & Minor Axis Shear Force.
These are called collectively as Ignorable Forces in Beam Design Settings > Design Tab (as shown below).

Users can set their preferred Ignorable Forces based on their own engineering judgement or calculations.

If the actual design forces exceeds the Ignorable Forces values, the beam will be marked as "Fail" with red cross even the reinforcement bars provided is sufficient.
When you double click these beams in Beam Reinforcement Design to open Reinforcement Data Dialog or select the beams in plan view, right-click select "Beam Section Design", it will give you the Warning(s) stating that the design axial tension, minor axis shear forces, and/or minor axis bending moment exceed(s) the ignorable limits.
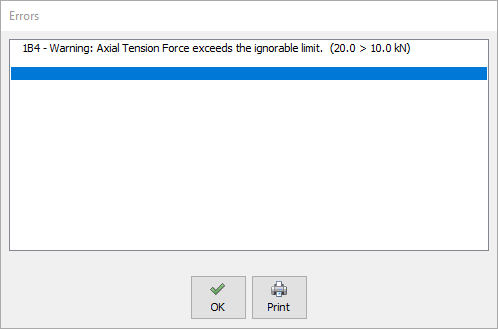
Also, you may find the warning message in the "Storey Beams" under the "Design" tab after done designing the beams by batch mode:
Why does a beam have high tensile / ignorable force?
There are many reasons why a beam may experience high tensile or other ignorable forces :
1. The beam is not connected to a slab and hence not restrained by the diaphragm which is formed by slabs, hence it is free to elongate or bend within the floor plane, as hence tensile / minor bending & shear force is produced.
2. Under high loads, especially lateral loads, beams that are not restrained by diaphragm may develop high ignorable forces
3. Wrong modelling - if the beam is unstable, e.g. unsupported - the entire model may collapse, leading to unexpected or erroneous forces
What can be done if beam fails ignorable forces
There are several course of action that can be taken when beams failed by ignorable forces :
- User should manually check the beam capacity by his/her own calculations.
- If the user deem the beam actually pass the ignorable force, he can manually over-ride the failure by going into the Interactive Beam Design and choose "OK" to force the beam to a "Pass" (as shown below)
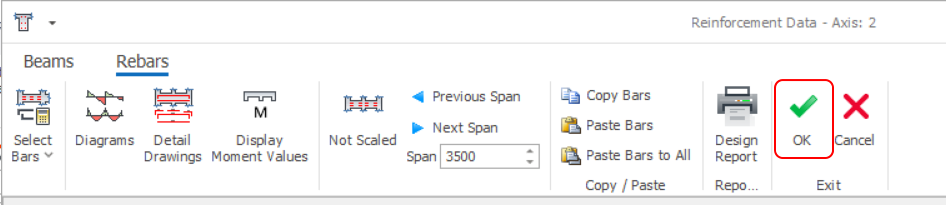
- The user can also change or increase the Ignorable Forces limit values. For example, one can calculate a typical beam tensile capacity by equation below.
- Beam Tensile Capacity = (Number of bars x Cross sections area of each bar x Yield strength of the steel)
- This way, more beams can pass automatically, if the design tensile force is less than, then manually input Ignorable tension force.