To create the welds, please follow the instructions below:
a. Ensure all end of the pipes are within the connecting member section. In case of the pipe is protruded out from the connecting member, we can offset the member end by adjusting the x, y, z offsets in member properties with utilizing the Draw Frame Coordinate System (Local Axis System) of the member.
Steps and demo GIF below:
- Select the protruded pipe, double left-click to access the member properties.
- With the pulldown list right beside Draw Frame Coordinate System, select either "For Detailing" or "For Analysis & Design" to check the member local axis indicator.
- The end where the indicator seats on will be the "Start" whereas the other end will be the "End". Based on the Arrows (Red = x, Green = y and Blue = Z), offsets can be done easily.
In the example below, we simply set offset for x = 50mm (can be any number as long as it is within the chord pipe), just to ensure the pipe does not protruded out for connection modelling purposes.
b. Now, click the “Boundary Cut” command to trim the selected pipe based on the chord pipe.
You may always press shortkey, ALT + D, to switch object view mode instantly to check the members.
To understand more on how to utilise Cut Operations, please refer to this article : Cut Operation
c. Then, go to "Steel" tab > Weld > "Fixed Weld” command to create the weld.
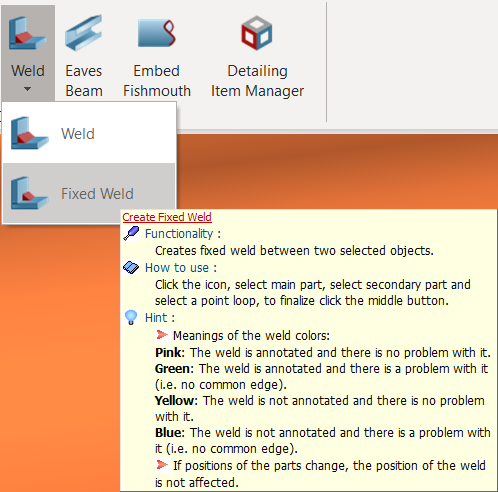
- Hold Shift + left-click on the “Create Fixed Weld” command to adjust the property of the weld,
For example, you may want to adjust the grade of weld, size and weld type to "All Around".
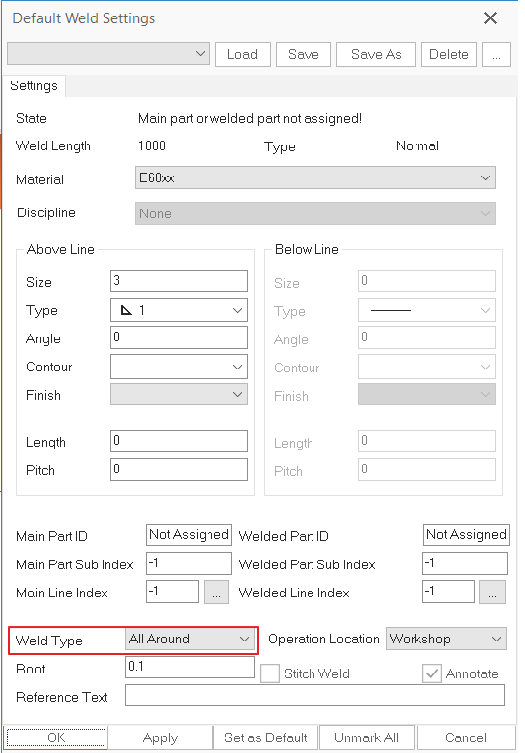
- Then, click the “Create Fixed weld” button > Select the chord pipe (main profile) > Select the connecting pipe. Remember to press “ALT+D” to switch to “Wireframe mode”.
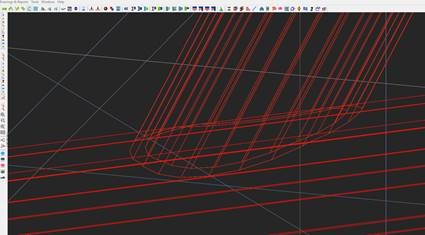
- Now, you can start to pick the points along the edges where the welding to be formed.
You have to pick the “first point – second point – second point – third point - ……N point …- first point” > Press you mouse “Middle button” (i.e. the roller) to end the insertion.
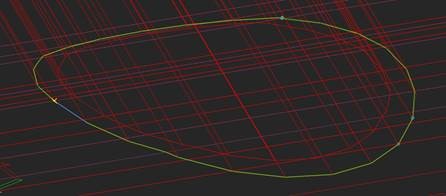
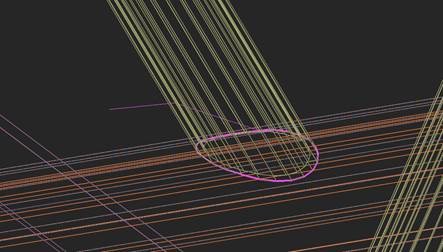