Introduction
During modelling
structures, there may be situation where the beams insertion point is offset from columns
insertion point. In other words, the beam end node may not coincide exactly with the column node.
In ProtaStructure, as long as beams end node (insertion point)
falls within the boundary of the column, rigid links will be auto generated to ensure the beam is supported by the
column.
We will use a simple model to illustrate this.
Simple test model
Figure 1
Four simply supported
beams are created with different end nodes insertion point:
- Beam A - Both beam end
nodes intersect with column nodes
- Beam B - Both beam end
nodes are at the column edge
- Beam C - Beam gridline
offsets from column gridline
- Beam D - Beam gridline
offsets from column gridline and beam nodes are at the column edge
Parameters:
Beam span : | 5m |
Beam self-weight : | 3kN/m |
Dead Load : | 10kN/m |
Live Load : | 30kN/m |
Analytical Model & Results
The model is analyzed and the Analytical Model view is accessed to verify the analytical wire-frame created by building analysis. 
Figure 2
With reference to the above analytical view :
- The blue line is the analytical wireframe of the beams and columns.
- The dark blue line is a rigid link which is automatically generated in the analysis to ensure the offset beam is supported by the column.
- The red line is the deflected shape.
- For model A, no rigid link is created as the insertion node of column & beam is the same.
- For model B, the rigid link is created to face of the column since the beam insertion node is at the face of the column.
- For model C, the rigid link is created out of the plane of the frame to the edge of the column.
- For model D, a diagonal rigid link is created from the centroid of the column to the corner edge of the column.

As long as the beam node (insertion point) is within the boundary area of the column, these rigid links will be automatically generated, so the the beam is properly connected to the column.
Frame Load
The frame load for G load case is turned to show the total calculated dead load, G on the beams. This includes the selfweight & any user-defined uniform load on the beam.

Figure 3
There are differences in the frame loads as follows :
- Beam A & C :
- The user-defined UDL of 10 kN/m is applied to the center-line / insertion point of the column.
- The self-weight of the beam of 3 kN/m is taken to the edge of the column, which is more accurate.
- This explains the change or "kink" in frame value at the face of the column, from 10 kN/m to 13 kN/m.
- Beam B & D :
- Both the user-defined UDL & self-weight of beam is taken to the insertion nodes of the beam ends.
- Hence there is no "kink" in the frame load along the entire span of beam.
Similarly, frame load for Q load case is turned on, to show the user-defined live load on the beam (as shown below) :
Figure 4
From the above frame load diagram :
- As expected, there is no change or "kink" in the Q load frame values. A single value of 30kN/m is applied between the end nodes of the beam.
- The only difference is the length on which the uniform load is applied, due to the different insertion point used.
Axial Load
The axial load diagram due to ultimate load combination 1.4G + 1.6Q is turned on as shown below :
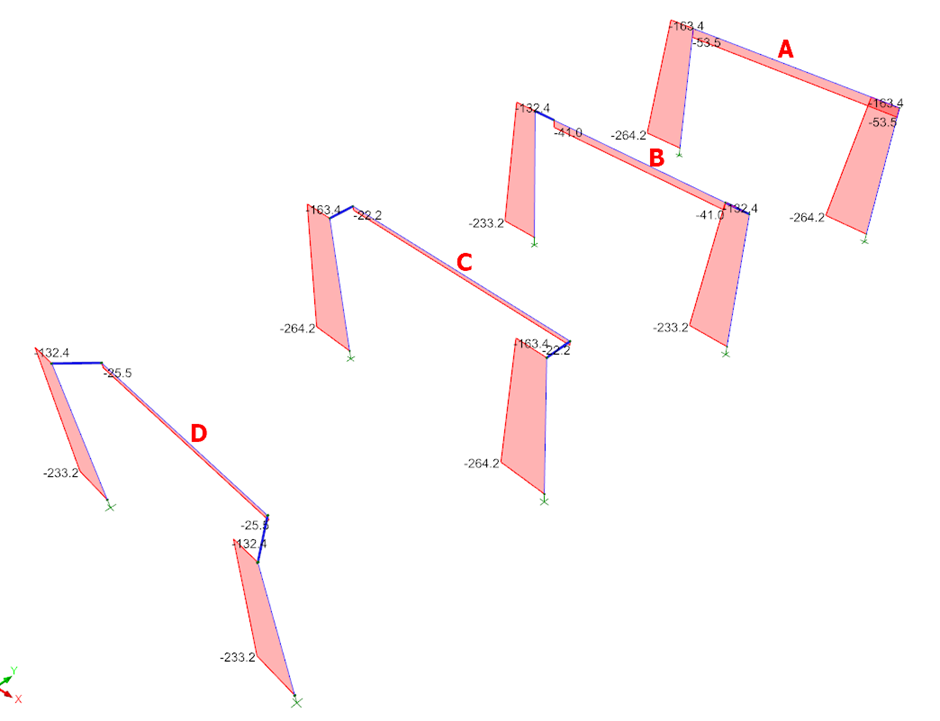
Figure 5
There is difference in the column axial load between the models :
- The column supporting beam A has equal axial loads as column supporting beam C.
- The column supporting beam B & D has the same axial load & is lower than that of A & C.
- This can be explained by referring to the frame loads as shown in figure 3 & 4 :
- Column supporting beam A & C has higher axial load as the frame loads are taken from center-line of the column; hence the load length & total load is higher.
- Column supporting beam B & D has lower axial loads because the frame loads are taken to the face of column; hence the load length & total load is smaller.
Moment M33
The major moment M33 diagram, i.e. in the plane of the frame, due to ultimate load combination 1.4G + 1.6Q is turned on a shown below.
Figure 6
There are differences in the moment diagrams :
- Model A :
- The bending moment diagram is taken to the centerline of the column which coincides with the beam nodes.
- This is the simplest center-line wire frame model which will serve as base of comparison.
- Model B :
- The moment values for beam is lower, compared to Model A, because the frame loading length is the face of the column, i.e. shorter - hence the total load on beam is lower.
- The moment of the column is higher due to additional eccentric moment generated by rigid link. The eccentric moment generated is equivalent to the shear force at the beam end multiplied by the rigid link length.
- Note the beam end moment value is not the same as top column moment due the rigid link.
- Model C :
- The bending moment profile is similar to model A.
- However, the values are smaller due to the existence of the rigid links - the analytical model is thus different & not comparable considering additional 3D effect
- The 3D effect can be seen in figure 4 : Model C is also deflection out of the plane of frame.
- Model D :
- General behavior is similar to Model C, except a diagonal rigid link is created to the corner edge of the column.
- However, the maximum hogging moment of beam is considerably smaller than Model C, due to the shorter beam length & hence lower total load.
- The maximum moment in the column is higher due the the longer rigid link, resulting in higher eccentric moment induced by the offset beam.
Moment M22
Moment M22 is the minor moment of beam, out of the plane of frame. It is also the moment of the column in the other direction, in this case, also out of the plane of the frame.
The M22 moment diagram due to ultimate load combination 1.4G + 1.6Q is turned on a shown below.
Figure 5
With reference to the diagram above :
- Beam A & B : No minor moment induced as the analytical model is fully in a single vertical plane.
- Beam C & D : There are moment induced in the column with offset beams (Beam C and Beam D) in
minor direction (out of the plane of the frame).

Users must be aware of this additional eccentric moment generated in the columns with offset beams.
All moments, eccentric or not, which will be automatically considered in member design.
Conclusion
From the above investigation & result, we can summarize & conclude the following :
Model A & B : Model A is preferable to model B due to following reasons :
- Model A has no rigid link generated, the same maximum hogging moment in the beam is transferred to the column.
- Model B introduced complexity of rigid link unnecessarily - resulting in lower hogging moment at beam ends.
- It is easy to verify model A result with hand calculation & any other analysis program.
- Model B result cannot be verified using hand calculation due to rigid links. Results can only be verified with other 3D analysis program that is capable of generating rigid links.
Model C & D : Model C is preferable to model D due to the following reasons :
- Model C max hogging moment at beam end tallies with moment at the column end.
- Model D beam max hogging moment at beam end is much lower than model C, the design will be unconservative.
- Overall Model C results proves to be more reasonable & in-line with traditional assumptions.

Generally, it is recommended to have as few axis intersection as possible, to ensure not too many unused nodes are created.
Model A & C requires less number of axes & hence nodes to be created. As such, a simpler analytical model is created.

Rigid links
are not auto-generated for shear walls. Beam insertion must coincide exactly
with the wall insertion axis.
Related Articles
Working with RC Beams
Different Type of RC Beam They are different types of reinforced concrete beam. The icons are accessible from the Modelling tab, RC Beam drop down list. Foundation Beam A foundation beam is a reinforced concrete beam modelled in ST0, which is always ...
BIM Links & Analysis Links
The BIM (Building Information Model) ribbon contains import & export functions for model, drawings, document and analysis software links. IFC Import We keep our commitment to continuously develop our IFC import and export links. We have continued ...
How to model a Transfer Beam supporting discontinuous columns and walls
Before proceeding with the modelling of the transfer beam, it is important to understand how the physical model translate to an analytical model when building analysis is performed. The physical model is what you see on the modelling screen where all ...
Castellated Beams
A castellated beam is created by slicing an I-beam longitudinally along its web in a specific pattern. The goal here is to separate and rejoin the beam with a deeper web. Castellated beams offer increased depth compared to the original section, while ...
Beam Design Settings
General Beam design setting must be preset correctly before starting any beam design. This is to ensure the beams are correctly designed based on the project criteria & user preferences. To access the Beam Design Setting, user can: Go to "Building ...