Once we have finalized position of the steel members, we can start “connecting” the steel members, i.e. create connections. Connection can be created in two ways:
- Automatically using the connection macros from Macro Gallery or IntelliConnect
- Manually by using the Plates, Bolts, Welds & Cuts commands
The automatic connection macros will automatically create the appropriate connection. If internal forces are transferred from ProtaStructures, they will be automatically considered in the connection design.
Detail design check is performed for the following connections as per Eurocode 3, AISC (LRFD), AISC (ASD), BS 5950.
- Beam to Beam Connections: End Plate, Stiffened End Plate, Fin Plate
- Beam to Column Connections: End Plate, Stiffened End Plate, Fin Plate
- Beam to Beam End Plate Connection
- *Haunch Connection
- *Direct Welding Connection
- Apex Haunch Connection
- Simple Base Plate Connection
- Flange Plate Moment Connection
- Extended End Plate Connection
- Bolted Gusset Plate Connection
- Corner Bolted Gusset Plate Connection
- Welded Gusset Plate Connection
- Corner Welded Gusset Plate Connection
- Splice Connection
A detailed design report can be produced for the connections mentioned above, including geometric and capacity checks. In addition, intermediate calculations, references to appropriate clauses of the design code, and corresponding equations are shown for easy checking.
ProtaSteel has the feature of transferring data to IdeaStatica connection program. With this feature, connections created with macros and user-defined complex connections can be transferred to the IdeaStatica program and connection calculations can be checked with the finite elements method. For the above connection, the following basic material strength checks are performed:
- Plate bearing check
- Bolt shear & Bolt tension check
- Weld stress check
- Plate tension & plate bending check
The checks above are the basic material checks, not clause-by-clause code-specific checks. No design report can be produced. You are advised to perform your additional calculation checks if required.
The force used in the automatic connections are obtained from the higher of the two values:
- The critical design forces of the connected members imported from ProtaStructure
- User-defined Capacity Ratio in the Profile Properties > Detailing Definitions.
- Capacity Ratio = Design Force / Maximum Member Capacity (equal or less than 1)
- This approach prevents unrealistic design when the design forces are very small or negligible.
For example, in the determination of the number of bolts for a simple beam to beam fin plate:
- The critical design shear imported from ProtaStructure is 30 kN. This requires 1 number of bolts.
- The Shear Capacity Ratio of the beam is set to 0.3. This works out to be 100 kN which required two bolts.
- The final design shear force used is 100 kN and two bolts are chosen.
There is no checks or design at all for the following connections:
- Beam to Beam Angle Cleat Connection
- Fitting Connection
- Beam to Beam Fixed Connection
- Wind Column Connection
- Base Plate Without Design
- Knee Connection
- Beam to Wall Connection
- End Plate Splice Connection
- Purlin and Girt Connections
- Eaves Beam Connection
- Hollow Section Base Plate Connection
- Sag Rod Connection & Sag Rod Holes
- Welded Pipe Connection
- Welded Box Connection
- Apex Truss Gusset Connection
- Truss Seating Connection
- RC Column Truss Seating Connection
- Embedded Steel Connection
- Truss End Plate with Gusset Plate Connection
- Stiffened Base Plate Connection
- Batten Plate Connection
* Denotes : Check is provided, but will not automatically design the number of bolts and size of the plates. It will be provided with a default connection size and will require user to manually adjust the connection in the connection macro setting if the design has failed. For more information about the macro, please refer to : Overview of Connection MacroBefore performing connection design, the default design parameters can be reviewed :
- Go to File > Settings > Project Preferences
- Ensure that Design Standards for Connections is set to EC3
- General Overdesign Factor for Connections = 1
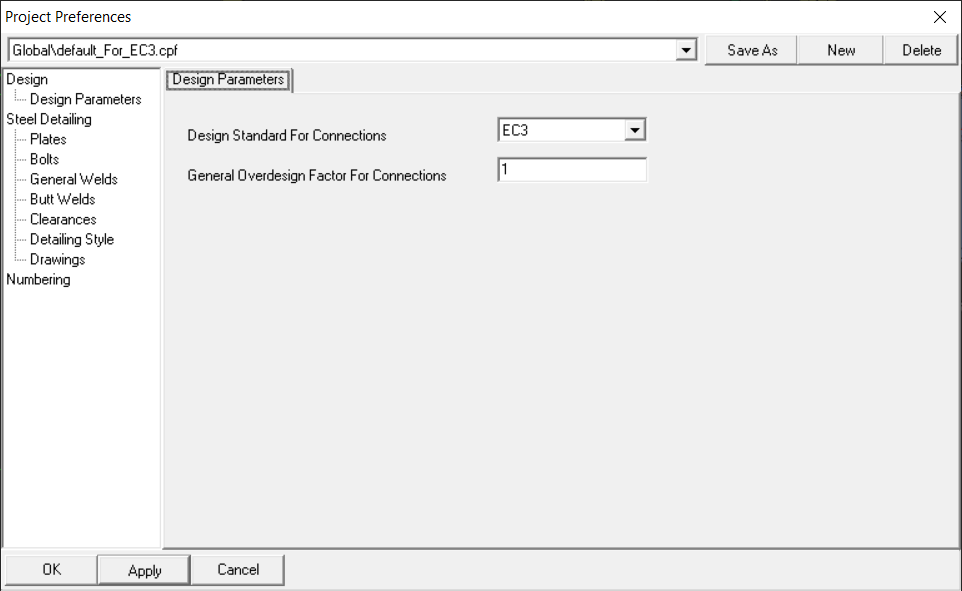
The connections will generally design for 100% of the member capacity. This setting works in combination with capacity ratios of the connecting members (changed via Profile dialog → Detailing Definitions). The Capacity Ratio is automatically calculated = Design force divided by the actual capacity of the member. Hence, Capacity Ratio x Overdesign Factor = Final Factor.
To prevent unrealistic design, a minimum capacity ratio may be imposed. For example, a minimum Shear Capacity Ratio of 0.3 is applied to all beams.