General
Beam Section Design allows user to access beam reinforcement data, beam report and etc.
To access Beam Section Design, user can either:
- Select a beam, then click on "Section Design"
under Beam tab, or - Select a beam, right-click to access shortcut menu and click on "Section Design"
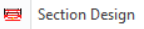
Beam Section Design consists of two tabs:
- "Beams” tab
- "Rebars” tab
Rebar Tab
By default, Rebar tab will be the main tab to be displayed when section design is opened.
In this tab, we have 2 sections:
Reinforcement Data Editor
In data editor, the result is dynamic which means when user edits rebars, the program will make changes on the calculations accordingly and immediately then provide instant feedback back onto the data editor. The provided reinforcement patterns system is tailored made to mitigate/eliminate the requirement of extra editing of the detail drawings.
This Editor consists of four sections:
- The schematic sketch of the beam
- Excess Steel Area
- Feedback Field
- Reinforcement Data Field
The values in these fields will be displayed in red when fails to satisfy/comply to the minimum requirements.
The schematic sketch of the beam
On the top of the form, the beams on the current axis are drawn schematically. The sketch shows the supports, beam labels, section dimensions, span lengths and required steel areas (at the top & bottom edge, at supports & span).

Red cross indicates that the beam design is section insufficient.
Excess Steel Areas
The “Extra As” values indicate the excess steel area provided by the supplied steel at the same location.
Feedback Field
Beam requirement checks and additional information can be found in this field:
- As-min (Top/Bot) : Minimum required steel area calculated based on the minimum steel percentages.
- B-Up Middle (Only With Bent-Up Pattern) : These fields display the possible width of the middle straight section of the bent-up bars.
If the reinforcement pattern used does not include the bent-up bars, these values will not be shown.
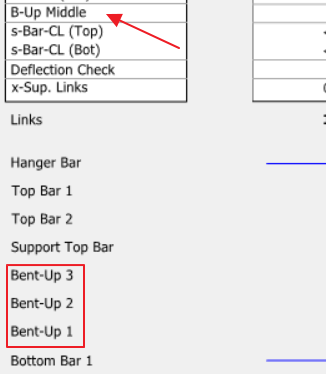
- s-Bar-CL (Top/Bot) : Center-to-center distance between the bars is calculated by formula:
S-Bar-CL = (Beam width - 2 (link size + concrete covers) - Nos of longitudinal bar * longitudinal bar sizes) / (Nos of longitudinal bar - 1). - Defl. Check Results : Beam deflection checks.
- x-Sup. Links Fields : Links in the support regions are calculated automatically and the calculated widths of the support regions are displayed here only when link at mid span is different compare to support link.
Reinforcement Data Field
The steel bar fields are arranged according to the reinforcement pattern selected. Navigation between the steel bar fields can be made by simply clicking the mouse button or by arrow keys.
Although we have set default reinforcement pattern, user can still modify each steel bar manually.
The automatically selected bars can be modified using the up/down buttons located adjacent to the selected steel bar field.
If any modification is made, recalculation of the supplied bars will be dynamically performed and other related fields will be updated as well.

Reinforcement Data Field - Hotkey
To navigate the steel bar fields between each span beam, user can:
- Scroll and select using mouse wheel, or,
- use the “Previous/Next Span” command
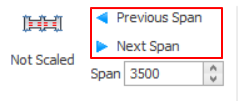
To modify rebar size, quantity or spacing, you can use the up/down buttons located on either side of the steel bar field. Alternatively, you can use the following short-cut keys to modify the steel bars:
F1
| Increase steel bar quantity
|
F2
| Decrease steel bar quantity
|
F3
| Increase steel bar size
|
F4
| Decrease steel bar size |
F5 | Increase steel bar spacing (Link only) |
F6 | Increase steel bar spacing (Link only) |
For example, to modify 2T16 to 4T14, user can press F1 twice and F4 once.
Reinforcement Data Field - Rebars Type
The available steel bar type in ProtaStructure are outlined below. All of the following bar type will not be visible in all reinforcement patterns. The necessary bar groups will be available depending on the selected reinforcement pattern. Reinforcement patterns can be selected using the “Select Bars” button.
- Hanger Bars : Hanger bars are used mainly with the bent-up bar patterns to provide links to be connected. These bars are used at the top layer in beams and in bottom layer in the foundation beams.
- The number of hanger bars is usually determined based on the width of the section.
- The hanger bars are usually lapped at mid-span when the selected quantity and size is the same as the neighboring spans.