General
Beam design setting must be preset correctly before starting any beam design. This is to ensure the beams are correctly designed based on the project criteria & user preferences.
To access the Beam Design Setting, user can:
- Go to "Building Setout" tab > "Settings Center" > "Beam", or
- Click on “Setting and Parameters” in the “Beam Section Design Summary Table”.

Most of the parameters defined in this section are stored separately for floor beams, rib beams and foundation beams.
Beam
Design
Basic design settings are controlled on this page. The settings may differ depending on which reinforced concrete design code is chosen. The figure below is for EuroCode :
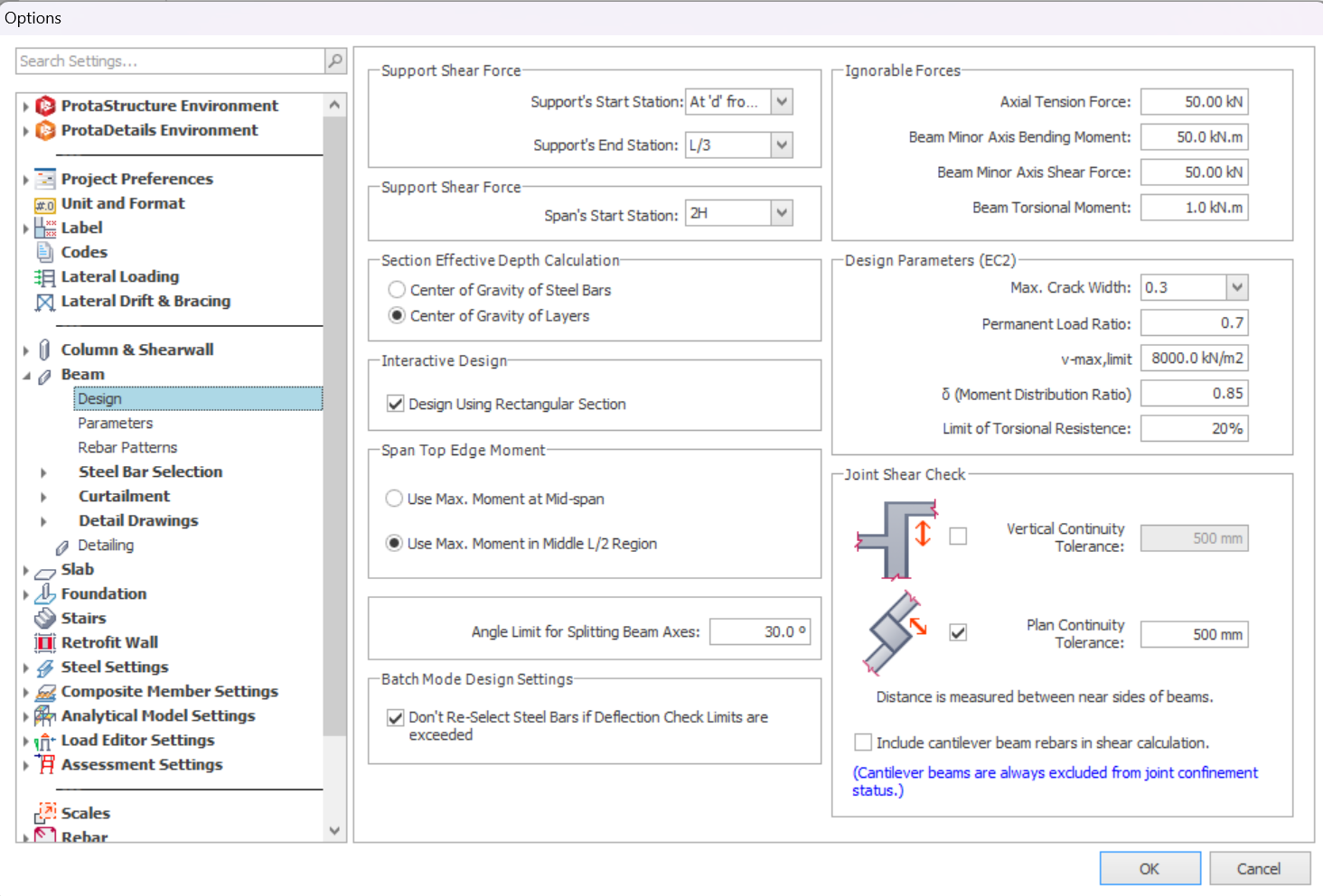
- Support Shear Force:
- Support's Start
Station : Design shear force may be calculated at “Column Face”
or at a “d” distance from column face. Here, “d”
is the effective depth of the beam.
- Support's End
Station : 2H, L/4, L/3 define the extent of support region. Here
"H" is the total depth of beam
- Span's Start
Station : 2H, L/4, L/3 define the extent of span region. Here "H" is the
total depth of beam
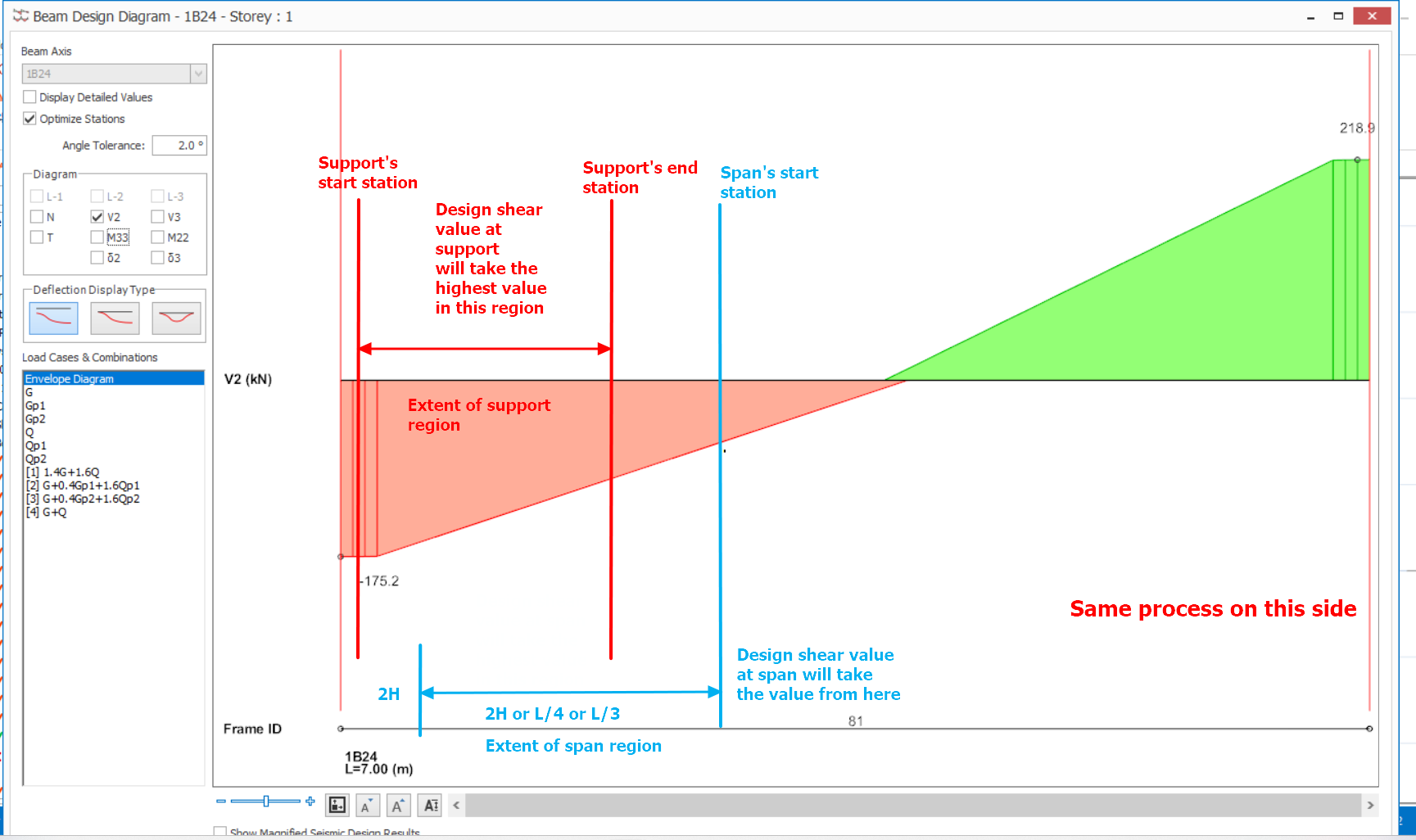
- Section Effective Depth Calculation : Effective depth of beam section will be calculated using either based on:
- Center of Gravity of Steel Bars : - The section effective depth will be determined based on the average centre of gravity calculated from each tension bars separately.
- Center of Gravity of Layers : - The calculation of section effective depth is based on the average of the distances of the steel bar layers (which is more conservative).
- Design Using Rectangular Section : Consideration of flanges during reinforced concrete design of beam section especially in span regions may yield more economical results. User may check this option to ignore the effect of flanges and use rectangular beam section in all beam design calculations.
- Ignorable Forces : Ignorable force values during the design process of the beams in the structure will be entered into these fields. If smaller design forces are obtained with respect to these values, then these forces will be ignored by the program. Please refer to this article for more details : Ignorable Forces for Beam Design
- Span Top Edge Moment : There are two options for in Span Top Edge Moment, which are "Use Max. Moment at Mid-span " and "Use Max. Moment in Middle L/2 Region ". User can choose either option to determine the maximum value for moment.
- Design Parameters (EC2) : Parameter available only when Eurocode template is selected.
- Max crack width : - Maximum allowable crack width for beam.
- Permanent Load Ratio : - Default value set to 0.7.
- v- max, limit : - Maximum allowable shear stress for beam.
- Moment Distribution Ratio, δ : - Referring to Eurocode 2, equation 3.15, the recommended ratio is 1.0, however Malaysia, Singapore, United Kingdom and Irish National Annex is set to be 0.85. User should decide the ratio based on own judgement. Default value is set to 0.85
- Angle Limit for Splitting Beam Axes : Allows user to set the angle limit at which connected beam axes with different orientation will be split (else combined). Refer to this article for more details : angle limit for splitting beam axes
- Joint Shear Checks : These settings will only appear if a seismic code is selected. For detail explanation refer : Beam-Column Joint Shear Design and Strong Column Weak Beam Checks
- Strength Reduction Factors : Only appears when ACI318 based code is chosen, which allows user to input reduction factors based on local requirements and practice (as shown below)

This page is used to set limits on the ranges and spacings of bars used in the design of floor beams, ribbed beams and foundation beams.
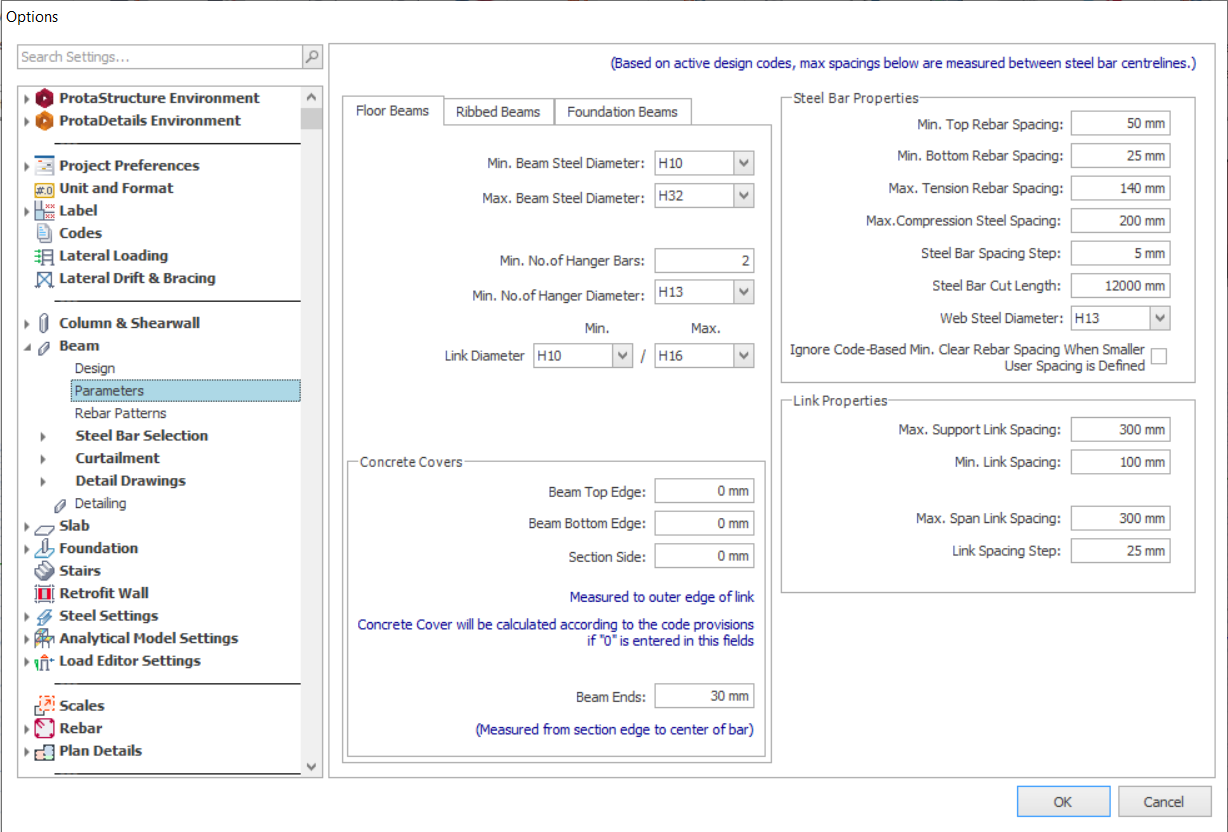
- General Properties :
- Min. Beam Steel Diameter : To set minimum allowable steel bar size. A smaller bar size will not be used during steel bar selection.
Note that, if you modify this section, you have to re-select the steel bars to reflect the changes. - Max. Beam Steel Diameter : To set maximum allowable steel bar size. A bigger bar size will not be used during steel bar selection.
- Min. Number of Hanger Bars : To set minimum number of hanger bars.
Note that, hanger bars will be used only in the steel patterns that make use of this bar group.
- Min. Hanger Bar Diameter : To set minimum diameter of hanger bars.
- Min./Max. Link Diameter : To set minimum and maximum allowable steel link size.
- Concrete Covers : To set concrete cover for beam top, bottom, side and beam ends. If 0 is input, the cover will be applied according to the design code. To check the cover in used, please refer to beam report or beam interactive design.
- Steel Bar Properties :
- Minimum Top and Bottom Steel Spacing : To set user defined minimum steel bar spacing. In code, minimum spacing will still be calculated based on clauses. If user defined spacing is smaller than min. requirement from code, program will take the greater value as the final min. spacing.
- Ignore Code -Based Min. Clear Rebar Spacing When Smaller User Spacing is Defined : Check this option to ignore the code calculated min. spacing and apply min. user defined spacing directly.
- Maximum Tension and Compression Steel Spacing : To set the maximum desirable steel bar spacing. Maximum steel spacing can be provided separately for tension and compression bars.
- Steel Bar Spacing Step : Spacing values will be incremented by the amount specified in this field during iterations.
- Steel Bar Cut Length : To enter the cut lengths of the steel bars. The length of the bars will then be checked against this value. Rebar exceeds this length will provide a lap.
- Web Steel (Side Bars) Diameter : To set minimum diameter that will be used for the side bars.
- Link Properties :
- Max. Support Link Spacing : To set maximum link spacing at support region.
- Min. Link Spacing : To set minimum link spacing at support region.
- Link Spacing Steps : Spacing values will be incremented by the amount specified in this field during iterations.
Rebar Patterns
This page is used to define the rebar patterns used in the project.
- Rebar Patterns : List of the standard rebar patterns provided here. User can select, modify and set the pattern as default.
- Rebar Types : Rebar types will be based on the "Rebar Patterns" selected. Select the rebar type to show and edit the curtailment options.
- Curtailment Options : - Edit the rebar length extension, layer and rename the rebar if desire.
- Pattern Summary : To summarize the current selected pattern in term of name and number of rebar type and layers.
- Set Pattern as Default : To set current selected pattern as default rebar pattern.
- Sample Drawing : To show sample drawing based on the current selected rebar pattern for better understanding.
- Beam Type : To switch between sample drawing of different beam type (Floor beam, foundation beam and ribbed beam).
- Span No : To show sample drawing of beam elevation with bars in different span number.
- Default Rebar Pattern : To show default rebar pattern set for this project.
Steel Bar Selection
Method
This page is used to apply more specific controls on the bar selection process.
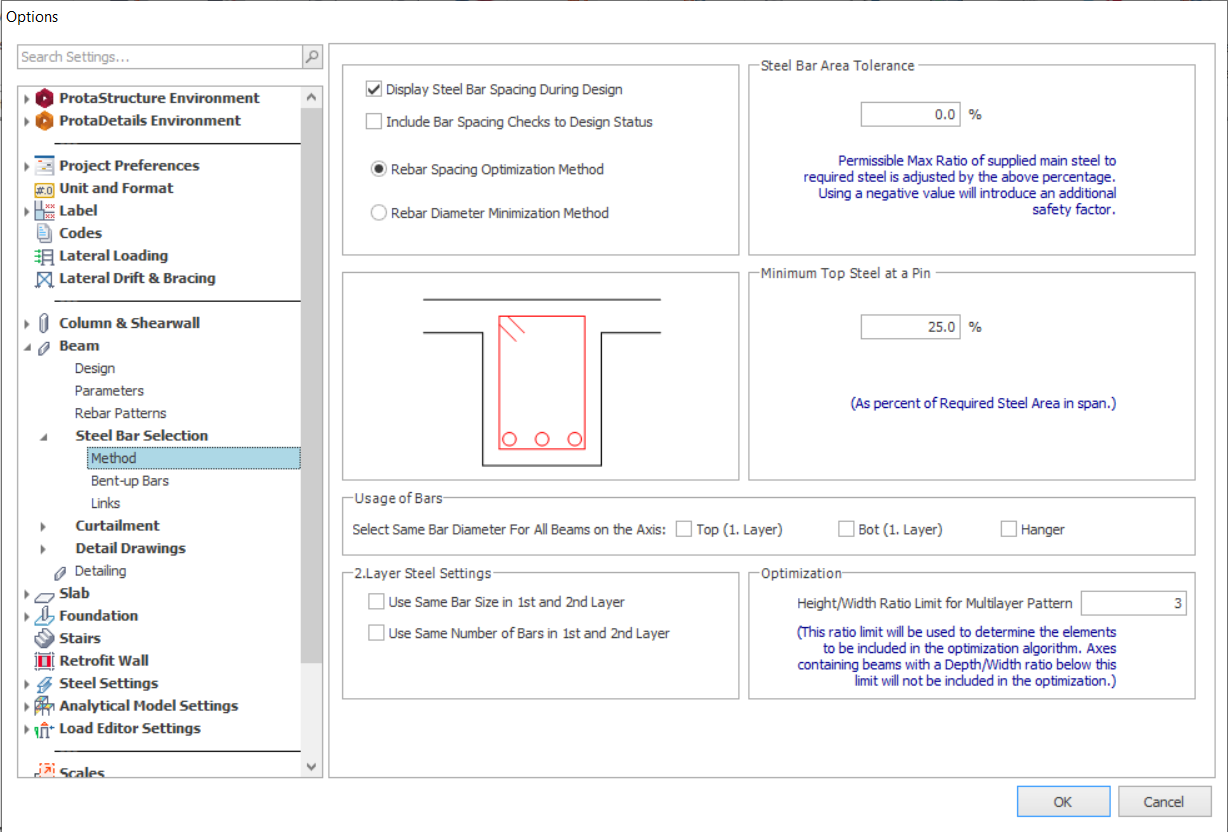
- General :
- Display Steel Bar Spacing During Design : If this option is checked, "Beam Section Design (Rebar tab)" will display "s-Bar " (the clear spacing between the bars) instead of "Min-bw " (minimum beam width that the bars will fit with minimum allowable clear spacing).
- Include Bar Spacing Checks to Design Status : Beam design status to include bar spacing check. If spacing check does not pass, design status will show fail.
- Rebar Spacing Optimization Method / Rebar Diameter Minimization Method : When performing auto-design, method selected will be prioritized.
- Steel Bar Area Tolerance : Introduce tolerance for required steel in the beam sections. Positive % tolerance in this field will result in the design providing less steel than required. Likewise, negative % tolerance values will yield greater steel areas than required (i.e. additional safety factor).
- Minimum Top Steel at a Pin : If hinge mechanism is defined at the beam ends, user can enter the minimum top steel area required at support regions with a percent of the bottom required steel area at mid span region.
- Usage of Bars : To standardize rebar size for all beams in the same beam axis based on the ticked options. (In certain case, such as support region will require larger rebar to satisfy the required steel area, the program will still automatically up size the rebar.)
- Layer Steel Settings :
- Use same Bar Size in 1st and 2nd Layer : To standardize rebar size in first and second layers of the beam.
- Use Same Number of Bars in 1st and 2nd Layer : To standardize rebar number in first and second layers of the beam.
- Optimization :
- Height/Width Ratio Limit for Multilayer Pattern : To optimize rebar layers pattern using "Optimize Rebar Layers“ button in "Beam Section Design Table - Design Tab". Only beams that are equal or exceeding this ratio will be included in the optimization process (optimize the Utilization Ratio) and auto-assigned the multi-layer bar pattern.
Bent-up Bars
This page is used to apply specific controls to the Bent-up Bars.
Beam Type : To switch bent up bars setting between:
Floor Beams
Ribbed Beams
Foundation Beams
Bent-up Bar Control Acc. to Beam Span (section 1) : To define the design parameters of bent up bar based on the beam span.
Bent-up Bar Control
No. of Bent-up Bars
Bent-up Bar Min. Middle Length
- BU Bar Angle
Bent-up Bar Control Acc. to Beam Span (section 2) :
Double Bars Min. Length : To preset bent up bars minimum length for double bars.
Triple Bars Min. Length : To present bent up bars minimum length for triple bars.
Links
This page is used to apply specific controls to the Links.
- Link Quantity Control :
- Double Bars Min. Width : Beam auto design to allow double links when beam width, "bw" is greater than the user defined minimum width.
- Triple Bars Min. Width : Beam auto design to allow triple links when beam width, "bw" is greater than the user defined minimum width.
- Link Pattern : To select link standard pattern for beam design.
- Use Special Torsion Links : To use torsion links when necessary.
- Rib Links :
- Type : To select link type for rib beam.
- Extension : To define the extension length of the link end towards the flange.
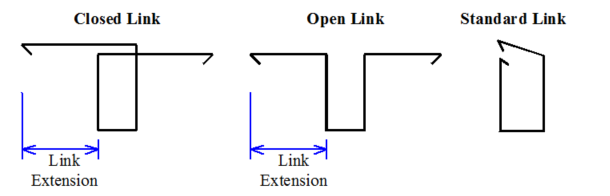
- Design Link Spacing at Supports : Check option to design link spacing at the support region based on the "Link Spacing at Supports Settings". Otherwise, same link size and spacing will be used in span and supports calculated based on the maximum design shear force.
- Link Spacing at Supports Settings :
- Use Same Links for Support and Span :
- This is more applicable when "Standard Pattern 7" is selected for RC beam rebar curtailment, where the top and bottom lap splices will always be made in the mid-one-third region of the beams.
- When the option is checked, the support link spacing will also be applied to span links, resulting in an overall confined beam in all spans (as shown below)
- Same bar size at supports and span : Check this option to use same bar size in supports and span regions.
- Use the same diameter on both supports : Check this option to use same bar size in both left and right supports regions.
- Fixed Support Region Width (2h) : To fix support regions length to be exactly 2 times the beam section height, "h". Otherwise, the regions length will comply to "Min. Support Region Width" option.
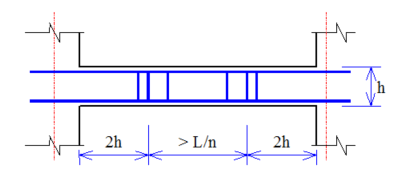
- Min. Support Region Width (Critical Zones) : To set the minimum support region width to "0", "L/3", "L/4" or "2h". L is defined as the clear span of the beam ; h is the overall section height of the beam.
- 0 means no confinement zone will be used even if the support links are specified.
- The confinement zone (critical region) length will be calculated according to the one of selected L/3, L/4 or 2h.
- Min. Span Region Width Options : When mid span region is less than the minimum set value here, the support links will be span throughout whole beam including the span region.
- The Minimum Support Zone Length has priority over Minimum Span Region Length. ProtaStructure will make sure that support zone length preference is reflected to detailing first.
- In the detail drawing above, the beam clear length is 4800 mm. Minimum support length is specified as L/3 so the critical zone detailing is done to 1600 mm. Although the minimum span length was set to L/2, ProtaStructure did not have any choice but the use the remaining 1500 mm as the support length. The residual 100 mm accounts for the offset of the first and last links from the support face.
Curtailment
Steel Bars
These settings affect how the reinforcement is curtailed.
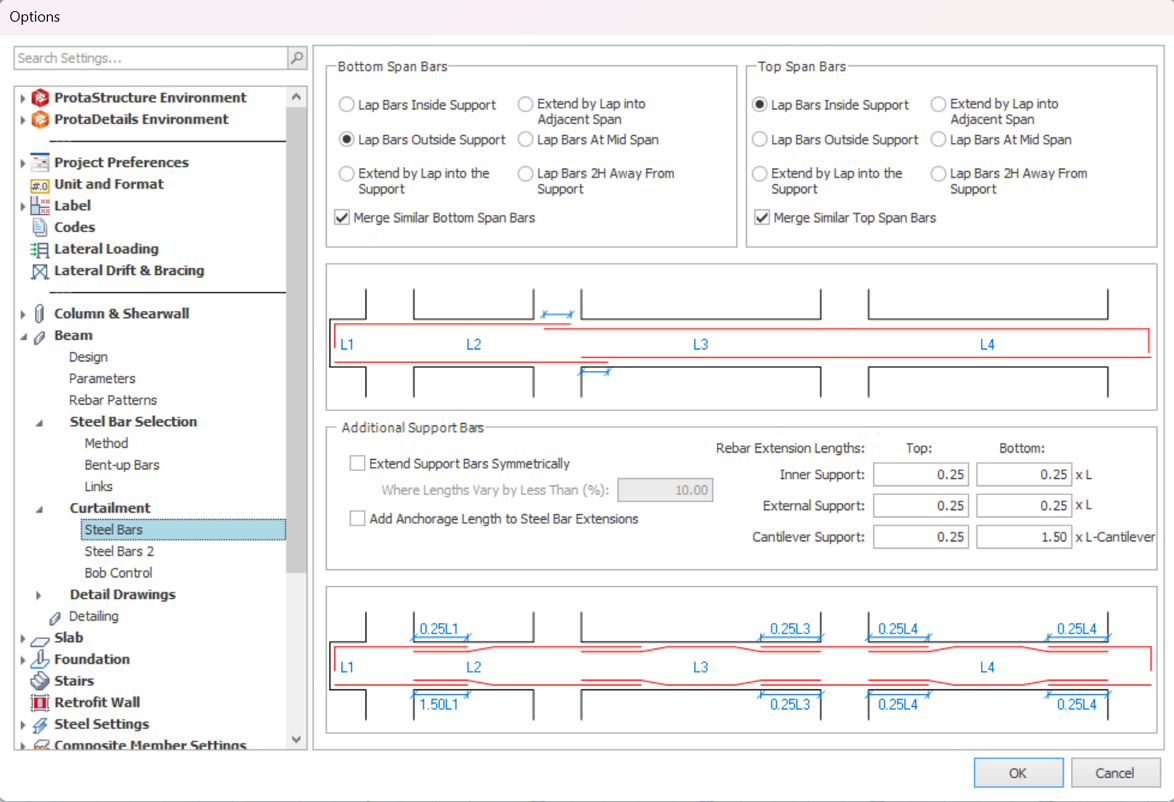
Bottom Span Bars :
Lap Bars Inside Support : To lap the bottom bars in the middle of the support region.
Lap Bars Outside Support : To lap the bottom bars to the right or left of the support region. The bars will be lapped at the side of the support where the bottom bars are smaller. If the bottom bar sizes are the same in both adjacent spans, then they will be lapped to the right of the support region.
Extend Lap into the Support : To extend the bottom bars into the support region by a lap distance after the inner face of the support.
Extend by Lap into Adjacent Span : To extend the bottom bars through the support region and extend them by a lap distance after the outer face of the support. This option is used generally in earthquake regions to provide more anchorage for the bottom bars.
Lap Bars At Mid Span : To lap the bottom bars in middle of span.
Lap Bars 2H Away From Support : To lap bottom rebars at distance 2 times overall beam depth from support. This curtailment option is necessary and useful especially for the special and intermediate seismic moment resisting frames.
Merge Similar Bottom Span Bars : To merge similar bottom steel bars.
"Similar bars" must have both quantities and bar sizes must be equal. Merging may be restricted due to geometric constraints and may not be successful in all positions.
Top Span Bars :
Lap Bars Inside Support : To lap the top bars in the middle of the support region.
Lap Bars Outside Support : To lap the top bars to the right or left of the support region. The bars will be lapped at the side of the support where the top bars are smaller. If the top bar sizes are the same in both adjacent spans, then they will be lapped to the right of the support region.
Extend Lap into the Support : To extend the top bars into the support region by a lap distance after the inner face of the support.
Lap Bars At Mid Span : To lap the top bars in middle of span.
Lap Bars 2H Away From Support : To lap top rebars at distance 2 times overall beam depth from support
Merge Similar Top Span Bars : To merge similar top steel bars
Merge Similar Bottom Span Bars : To merge similar top steel bars.
"Similar bars" must have both quantities and bar sizes must be equal. Merging may be restricted due to geometric constraints and may not be successful in all positions.
Additional Support Bars :
Extend Support Bars Symmetrically : To extend the support bars to both spans symmetrically based on the larger effective span length. This happens when length vary at both span is less than the preset %. This is a conservative approach.
"Where if Lengths Vary by Less Than (%) " : If variation in spans is more than the given value, no symmetry operation is performed.
Add Anchorage Length to the Steel Bar Extensions : To add anchorage length to the calculated extension length.
Rebar Extension Lengths : Support bar extension length multiplication factor can be set using the field provided in this section.
Steel Bars 2
Further settings that affect how the reinforcement is curtailed.

End Support Curtailment Control :
Extend Top Span Bars to End Support : To extend the top span bars of the first and last spans to the end supports.
Don’t Use Top Span Bars : To remove top support bars at the end support. In this case the span bars will be increased as necessary.
Extend Bottom Span Bars to End Support : To extend the bottom span bars of the first and last spans to the end supports.
Don’t Use Bottom Span Bars : To remove bottom span bars at the end support. In this case the span bars will be increased as necessary.
Minimum Tension Lap Factor (BS8110, CP65 & HK codes only) : With this factor set at 1.0, extended lap lengths are only introduced in some cases but not others. Some users may prefer to increase this factor to 1.4 to standardize on the use of extended lap lengths throughout.
Max. Bond Quality Coefficient (Eurocode 2 only) : Acceptable input range 0.5 to 1.0.
In the bond stress calculation (Cl 8.4.2), the bond quality coefficient η1 can be either 1.0 or 0.7 depending on section depth. Where 0.7 is used the bond strength is reduced and laps are extended. Specifying a maximum of 1.0 for the Bond Quality Coefficient allows the coefficient to vary between 0.7 and 1.0 as required, hence lap lengths will vary accordingly.
Some users may prefer to specify a maximum of 0.7 (which actually fixes the coefficient at 0.7), the effect is to standardize on the use of extended lap lengths throughout. Further conservatism can be introduced in all lap lengths by using a value as low as 0.5.
Plain Bars Bond Quality Modifier (Eurocode 2 only) : Acceptable input range 0.1 to 1.0.
In the EC2 Cl 8.4.2 bond stress calculation, there is no factor relating to the rib type of reinforcement, and no guidance on what adjustments if any should be made for plain bars.
In ProtaStructure a factor “T " has been introduced (as in BS8110) to allow for this adjustment. It is the users responsibility to enter a suitable value for plain bars. (Until further guidance becomes available, Prota would suggest that as per BS8110 a value of 0.5 would be reasonable.)
Type-1 Bars Bond Quality Modifier (Eurocode 2 only) : Acceptable input range 0.1 to 1.0.
In the EC2 Cl 8.4.2 bond stress calculation, there is no factor relating to the rib type of reinforcement, and no guidance on what adjustments if any should be made for Type 1 bars.
In ProtaStructure a factor “T ” has been introduced (as in BS8110) to allow for this adjustment. It is the users responsibility to enter a suitable value for Type 1 bars. (Until further guidance becomes available, Prota would suggest that as per BS8110 a value of 0.8 would be reasonable.)
Minimum Anchorage Length : To set minimum anchorage length based on multiplier of bar diameter.
Top Bar Lapping Factor (Eurocode 2 Only) : To set lapping factor of top bar based on multiplier of bar diameter.
Bottom Bar Lapping Factor (Eurocode 2 Only) : To set lapping factor of bottom bar based on multiplier of bar diameter.
Bob Control
These settings affect how the bobs are controlled. "Bob" stands for Bending of Bar.
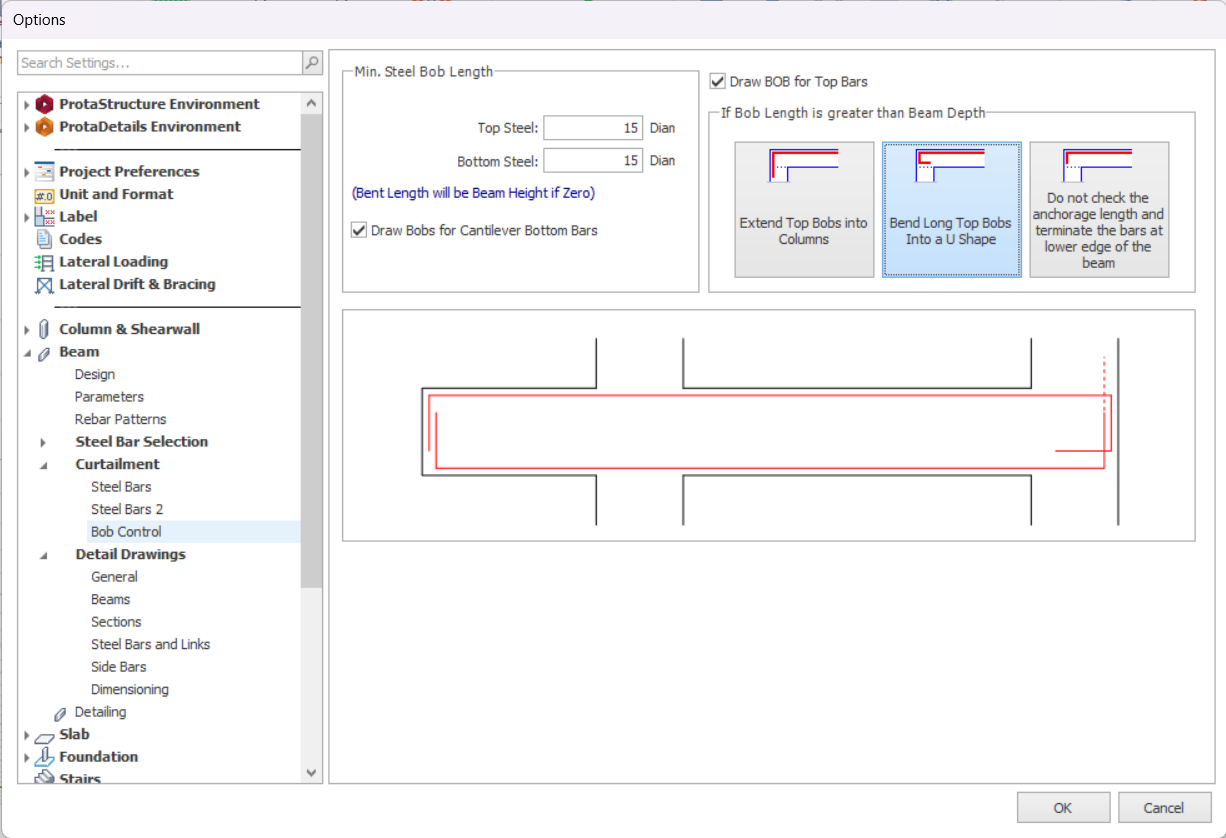
- Min. Steel Bob Length Control : To set the minimum bending of bars for top/bottom rebars based on multiplier of bar diameter.
- Draw Bobs for Cantilever Bottom Bars : Check this to have cantilever bottom bars to extend and bend up.
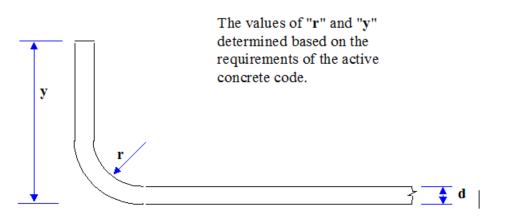
If Bob Length is Greater than Beam Depth : To choose the preferred anchorage detailing when the length of bending of bar is greater than the depth of the beam.
Care must be taken to check the position and dimensions of the connecting members to ensure valid detailing.
Detail Drawings
General
General setting for beam detail drawing can be configured here.
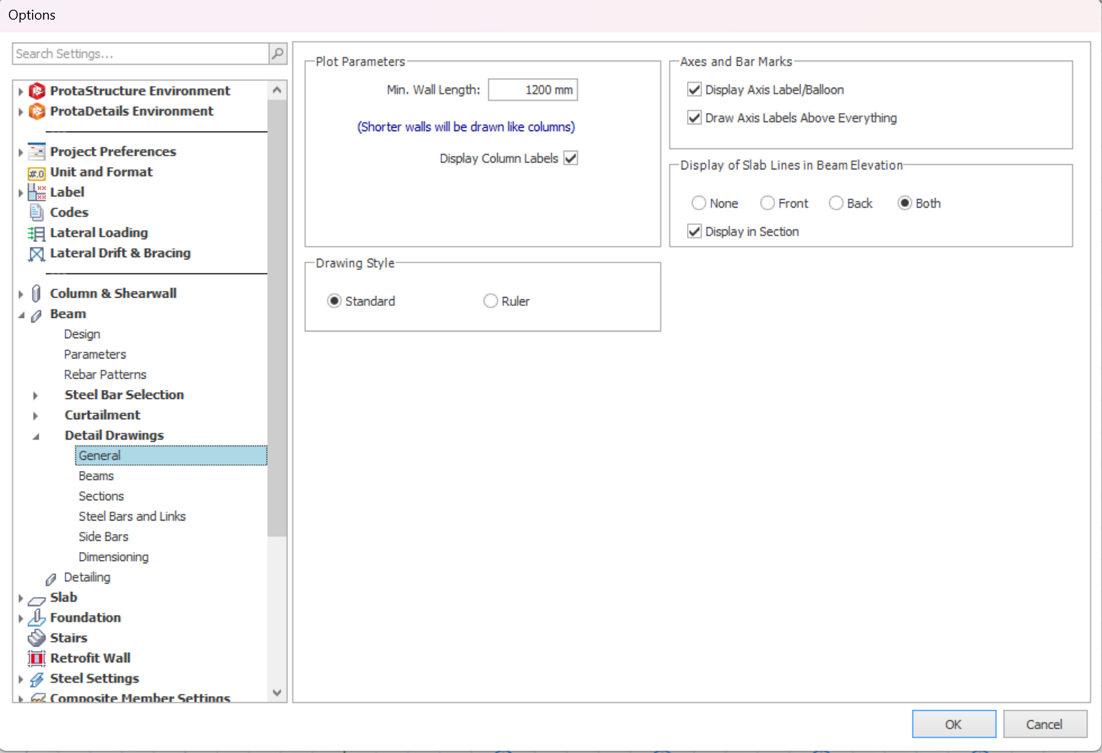
Plot Parameters :
Min. Wall Length : To set minimum wall length. For short wall length lesser than min. length will be drawn like column. Curtailment of the bars extended into the columns and walls are treated differently.
Axes and Bar Marks : Bar marks are determined and included with the bar label text if this option is set.
Display Axis Labels/ Balloon : By default, axis labels and circles at beam supports are drawn. Uncheck this option to suppress these labels.
Draw Axis Labels Above Everything : To draw axis label with axis balloon to be above of every other detail in the drawing.
Display of Slab Lines in Beam Elevation : To control the display of slab lines in the elevation view of the beams. If check "Both" option, the slab lines in front and back will be drawn. There are two different layers (Font Elevation Line / Back Elevation Line) to set the slab line color & properties separately.
Display in Section : To include slab line in beam cut section.
Drawing Style : To control the drawing style of beam detailing.
Standard : Usual schematic view of beam detailing.
Ruler : Rebars are drawn inside a box and a ruler is shown marking the bar end points together with the links.
Beams
Labelling related setting for beam detail drawing can be configured here.
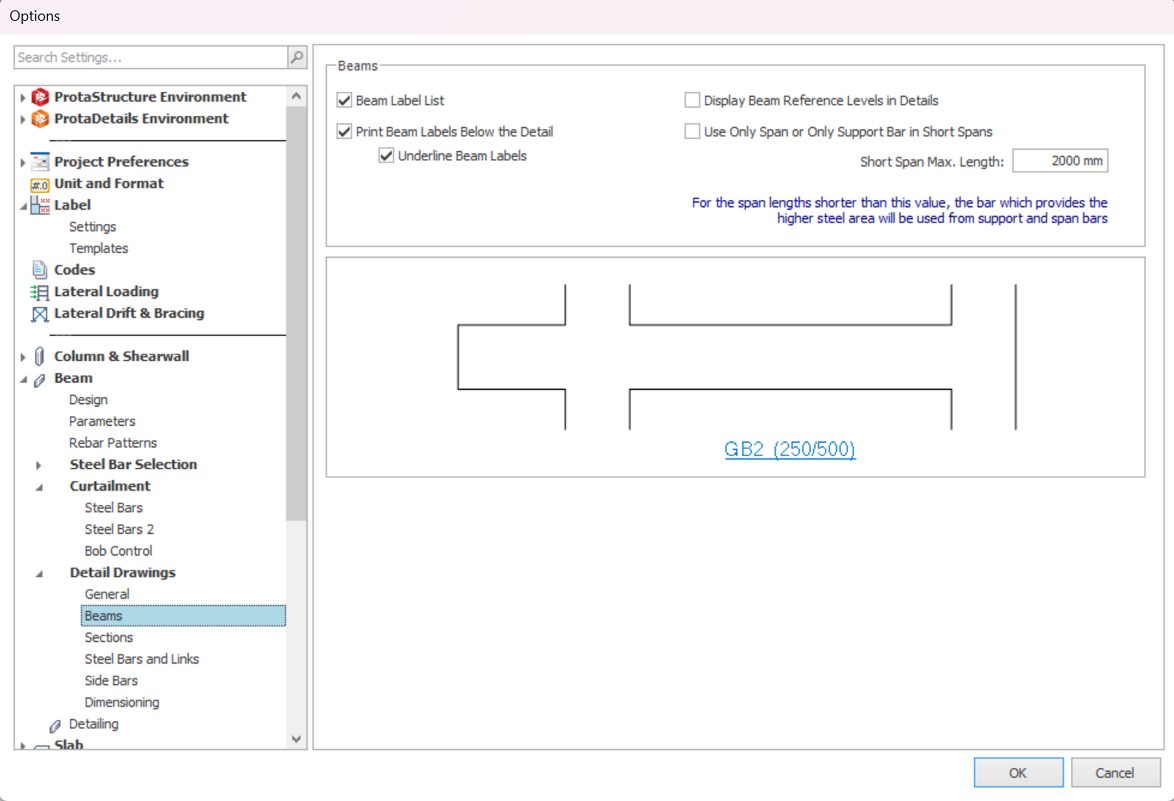
- Beam Label List : A list of beams in the sheet is generated during the preparation of the detail drawings. Uncheck to suppress the creation of this list.
- Print Beam Labels below the Detail : By default, beam labels are printed above the beam elevations. You can check this option if you want to have labels to be printed below the beam elevation
- Underline Beam Labels : - Beam label and section size texts will be underlined in the beam detail drawings.
- Display Beam Reference Levels in Details : To display the reference level of the beams in the elevation drawing. The reference level can be adjusted via the Building > Edit Storey form. This option is not valid for inclined beams.
- Use Only Span or Only Support Bar in Short Spans : To provides same rebars (span/support rebars, whichever higher in steel area) throughout the short span beam (more standardisation).
- Short Span Max. Length : - To set maximum beam span length limit to be considered as short beam.
Sections
Beam cut sections setting for beam detail drawing can be configured here.
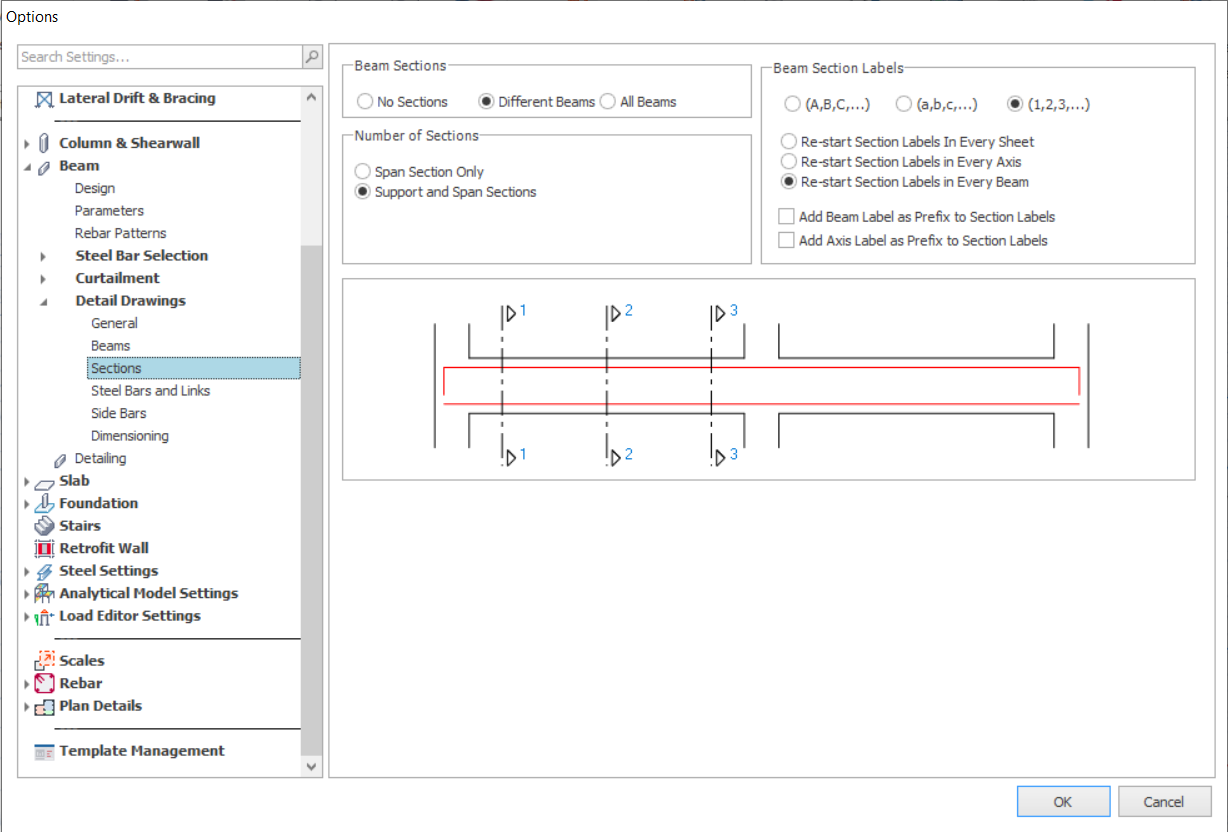
- Beam Sections : To control beam cut sections for beams.
No Sections : No sections will be included in the beam details.
Different Beams : Sections will be drawn only when a beam with different section dimension is found in a same beam axis.
All Beams : Section of all beams will be drawn.
Number of Sections : To control the number of sections to be provided for each beam.
Span Section Only : Only section at the mid-span of the beams will be provided.
Support and Span Sections : Three sections per beam will be provided. (2 at supports, 1 at mid)
Beam Section Labels : To control the arrangement and format of the section labels.
Re-start Section Labels in Every Sheet : Section labels will be reset for every sheet starting from “A”, “a” or “1 ”.
Re-start Section Labels in Every Axis : Section labels will be reset for every axis starting from “A ”, “a” or “1 ”.
Re-start Section Labels in Every Beam : Section labels will be reset for every beam starting from “A ”, “a ” or “1 ”.
Add Beam / Axis Label as Prefix to Section Labels : To prevent repeating labels, user may add beam / axis label preceding to section labels” (the labels will look like “(A-1B25) 1 - 1”, “(A-1B25) 2 - 2”, ... ).
Steel Bars and Links
Steel bar and links plotting setting for beam detail drawing can be configured here.
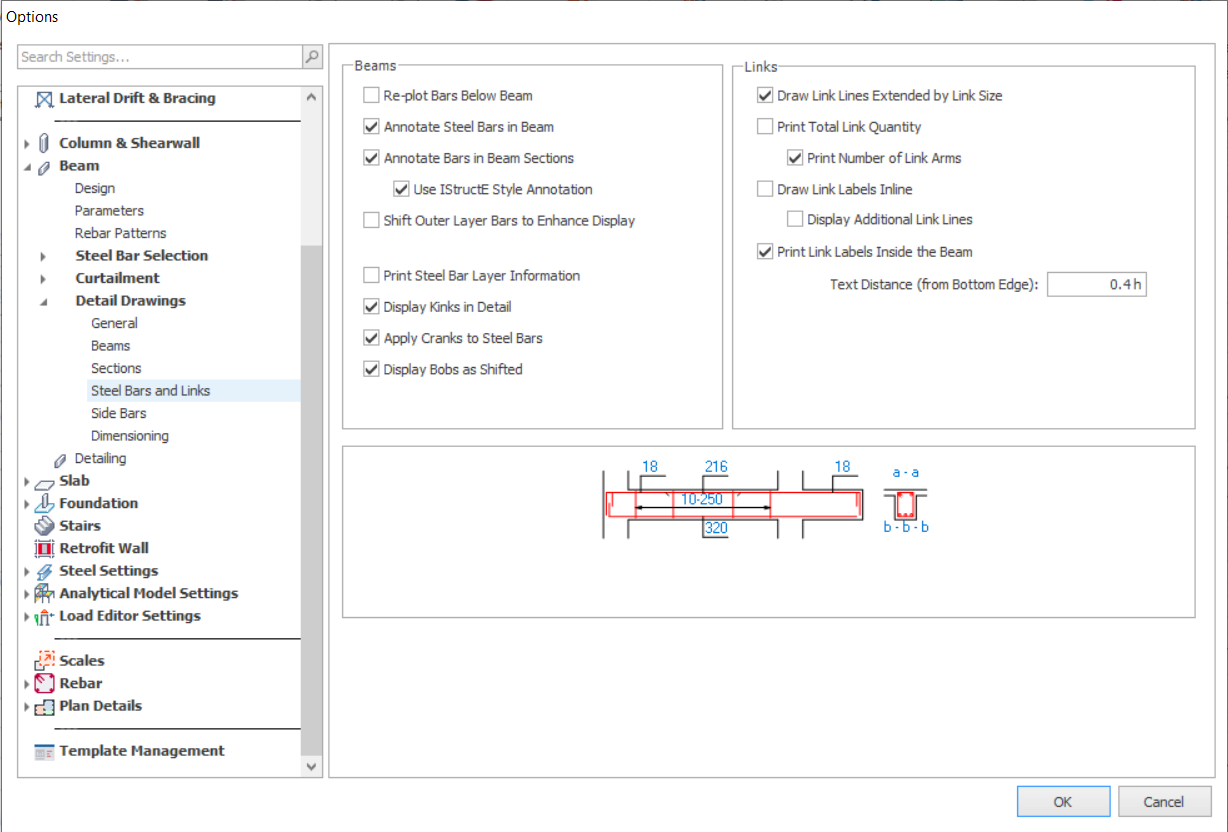
- Beam :
- Re-plot the Bars below the Beam : Beam rebars will be duplicated and re-plot below the beam elevation.
- Annotate Steel Bars in Beam : To annotate steel bar quantity, diameter and barmark information to the beam elevation.
- Annotate Bars in Beam Sections : To annotate steel bar quantity, diameter and barmark information to the beam sections.
- Use IStructE Style Annotation : To annotate section bars according to the IStructE Style to prevent overcrowded texts.
- Shift Outer Layer Bars to Enhance Display : To enhance the display by shifting any overlapping rebar layers (graphically) in the beam elevation drawing for easier understanding purposes.
- Print Steel Bar Layer Information : To print layer information (such as T1 for Top 1st layer bars) in bar label text.
- Display Kinks in Detail : To display kinks in the beam elevation drawings to mark the ends of the steel bars.
- Apply Cranks to Steel Bars : To apply cranks to the detailed drawings of steel bars.
- Display Bobs as Shifted : To shift out the bend of bars to enhance the display in the beam elevations for better understanding.
- Links :
- Draw Link Lines Extended by Link Size : To draw Link lines extended further than the top and bottom bars by half bar size + link size to enhance the beam elevation display.
- Print Total Link Quantity : To display total number of links with the link labels for each beam.
- Print Number of Link Arms : To display total number of links arms for each beam.
- Draw Link Labels Inline : To place the position of link label right at the center of the annotation line. Otherwise, it will be at above of the line.
Display Additional Link Lines : To display more links to express the spacing graphically.
Print Link Labels Inside the Beam : To annotate link labels inside the beam elevations. Otherwise, it will be annotated beneath the beam elevation.
Text Distance (from bottom edge) : When “Print Link Labels Inside the Beam ” option is checked, this field controls the distance that the link annotation line is positioned from bottom edge of the beam. The value entered in this field is a multiplier applied to the beam section height.
Side Bars
Side bars setting for beam detail drawing can be configured here.
Side Bars Arrangement : The program adds appropriate side bars based on the requirements of the active concrete codes for deep beams. Selecting "Along h " option will place the side bars equally spaced along the height of the beam, whereas "Along 2/3 h " option will place them equally spaced along the bottom 2/3 portion of the section.
Draw Side Bars in the Middle (when re-plotted below the beam) : To display side bars in between top and bottom reinforcement if "Re-plot the Bars below the Beam" is checked.
Display Only a Single Side Bar in Detail : To show a single indicative side bar, regardless of the total no. of side bars required to avoid too many elements in the final drawings.
Merge Similar Span Web Bars : To merge web (side) bars labelling of the adjacent beams if they have the same quantity and size of web bars.
Min Beam Depth for Side Bars : To set minimum beam depth to provide side reinforcement bar.
Dimensioning
Dimension related setting for beam detail drawing can be configured here.
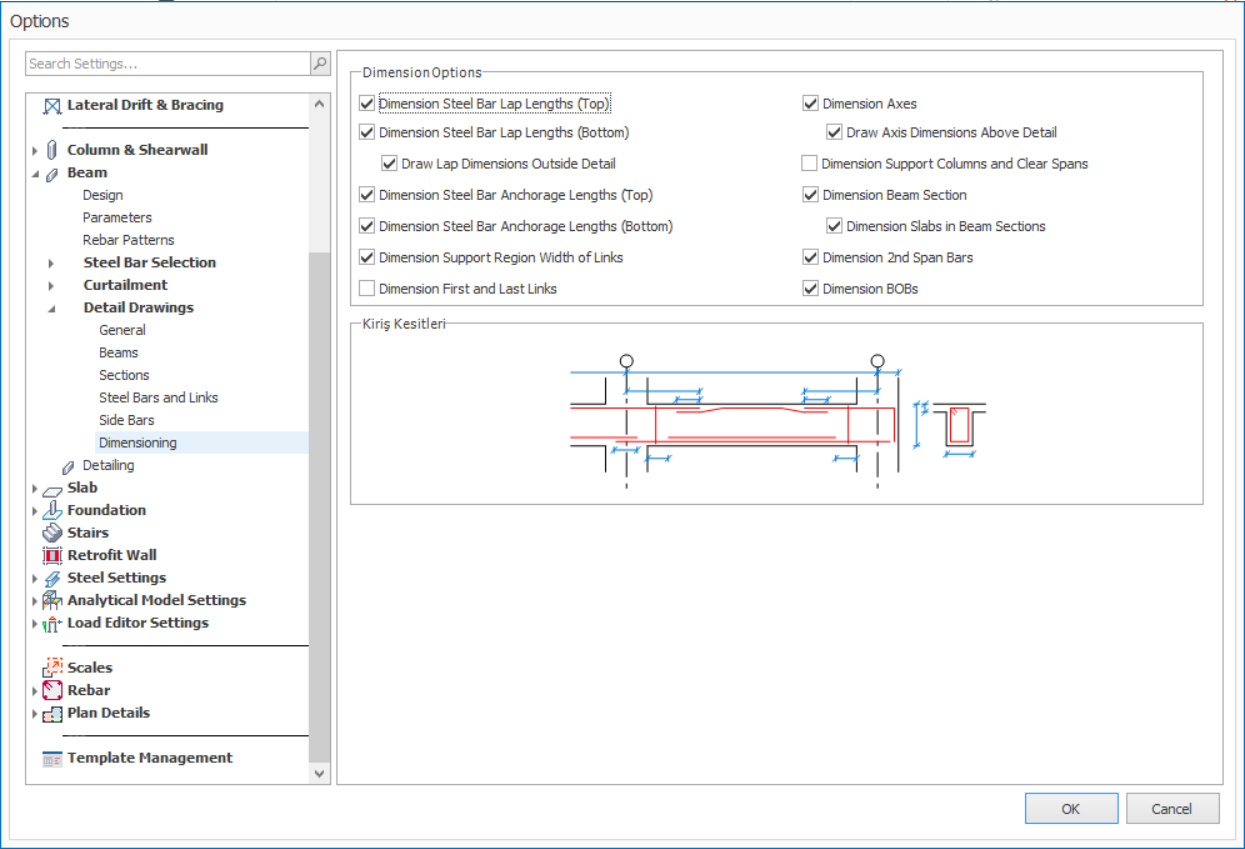
Dimension Options :
Dimension Steel Bar Lap Lengths (Top / Bottom) : To show lap length of top/ bottom rebars in beam detail drawing.
Draw Lap Dimensions Outside Detail : - To shift the lapping dimension outside of the beam elevation drawing.
Dimension Steel Bar Anchorage Lengths (Top / Bottom) : To show anchorage length of top / bottom rebars in beam detail drawing.
Dimension Support Region Width of Links : To show the dimension of link confinement zone of the beam.
Dimension First and Last Links : To show the distances for the first link to left support face and last link to the right support face for each beam.
Dimension Axes : To show distance of axis to axis for each beam.
Draw Axis Dimensions Above Detail : - To locate the dimension of axis to axis of the beam to top of the beam detail drawing. Otherwise, it will be located beneath the detail drawing.
Dimension Support Columns and Clear Spans : To show dimension of support columns and clear span distance for each beam.
Dimension Beam Section : To show beam sections dimension.
Dimension Slabs in Beam Sections : - To slab thickness/depth in beam cut section detail drawing.
Dimension 2nd Span Bars : To show dimension of the second layer span bars.
Dimension BOBs : To show dimension of the bending of bars.
Detailing
This tab relates to detailing presentation options.
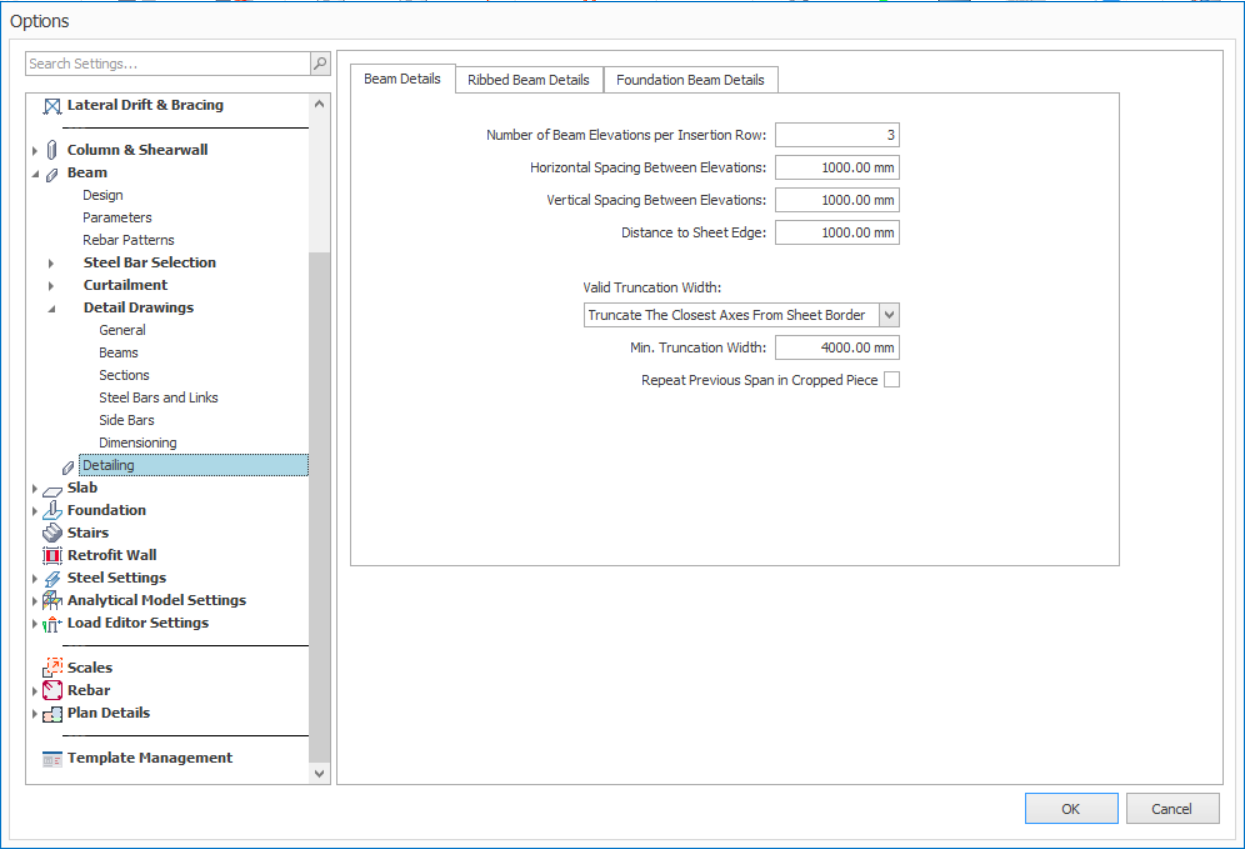
Beam (similarly, Ribbed Beam / Foundation Beam) Details :
Number of Beam Elevations per Insertion Row : To input desired row number of beam elevations per insertion when drawing the beam elevation without using sheet.
Horizontal/ Vertical Spacing Between Elevations : To input desired number for horizontal spacing and vertical spacing between each beam elevations.
Distance to Sheet Edge : To input desired distance between beam elevations and sheet edge.
Valid Truncation Width : Three truncation options for users to choose when insert beam details into sheet:
Don't Truncate
Truncate From Sheet Border
Truncate The Closest Axes from Sheet Border
Min. Truncation Width : To enter the minimum beam length to truncate.
Repeat Previous Span in Cropped Piece : This applies to "Truncate The Closest Axes from Sheet Border" only. When truncation happens, the last beam span at the truncation will be duplicated and become the first beam span when the beam elevation details continue at next the row after the truncation.