Before defining a Pad Footing:
- The building model must be completed and analysed, so that the column axial loads and moments are determined.
- The foundation storey 0 (ST: 0) must be set as the current storey.
In order to determine concrete and steel grades that will be used in the Pad Footing Design, you may go to Building Setout tab > Material > select Foundation Floor at the left hand list > select and edit concrete grade, rebar and/or soil at the right hand field.
To define a new pad footing:
- Select and right click column(s) to Insert Pad Footing at storey 0 via shortcut menu.
- More than one column may be selected. In that case, the Pad Footing Batch Design dialog will appear, showing the selected column & corresponding pad footings in a table format (refer section below for details).
- If a single column is selected, the individual Pad Footing Properties dialog will be displayed. Check the parameters in this dialog and press Design button to automatically design the footing.
- Desired footing size can be adjusted using Lx and Ly fields as well as other properties.
- Press OK button to close Pad Footing results dialog.
After completing the design of the pad footing, press the OK button to complete the insertion of the footing.

To create combined Pad Footing:
- Hold CTRL and click on columns to multi select the column stumps.
- Right-click to display the shortcut menu and select Insert Combined Pad Footing option.
- The Pad Footing properties dialog will be displayed. The columns will be combined into a single enlarged stump.
- Manually adjust the parameters and check the result below or press Design button to automatically design the combined pad footing.
- The pad footing will be designed for the combined loads from the column stumps in the group.
Combined Pad Footing is only suitable for a few columns very close to each; (example, less than 1m apart) as selected columns will be combined into a single stump & rigid footing is assumed.
If the columns are far apart, the analysis & design will be unreasonable. For example, the current footing only designs for bottom bars (for sagging moment) and not top bars (for hogging moment, which may be present if columns are far apart).
For situation where there are 2 or more columns in a straight line, you many consider Strip Footing, in which foundation beams must be modeled connecting to columns which in turn will be supported by footing. For more complicated arrangement of numerous columns that are far apart, we recommend you use FE Raft Foundation.
Combined Pad Footing is not suitable for shear walls due to same similar stated reasons; please use FE Raft Foundation. Refer to this article : FE Raft Foundation Overview In order to edit an existing pad footing:
- Select an existing pad footing.
- Right-click to select Properties from the menu.
- Modify or auto-design the pad footing
- Press the OK button in the Pad Footing properties dialog to update the model.
You can repeat this process to as many members as you wish. One member at a time can be edited by this method.
The Pad Footing Properties dialog will be loaded when the Insert Pad Footing option is selected or when selecting an existing pad footing by right-clicking and choosing the Properties option in the shortcut menu.
- There are 3 main category in this dialog named Geometry, Analysis and Rebars.
- You can click Design to auto design the pad footing.
- You can use the Generate Report button to view and transfer the pad footing design output of the current footing to document.
- Press Cancel if you wish abort the changes to footing.
Geometry Category
Geometry tab
The Geometry tab page comprises the pad footing dimension parameters such as Pad Footing Geometry, Column Dimensions, Pad Footing Eccentricity and Design Status and Result.
When changes to made in the dimension parameters, you will find changes in 2D and 3D view instantly.
Pad Footing Geometry and Eccentricity parameter can be adjusted based on below snapshot as a guideline:
- Footing Label : You can enter the label associated with the footing in this field. By default, a footing label associated with the column label will be generated. For example, “F1” will be generated if a footing for column “1C1” is to be created.
- Footing Depth : “Footing Depth” is the depth of the footing.
- Footing Taper Height : “Footing Taper Height” is defined as the height of taper occurs from the footing surface to the column surface.
- Concrete Cover : You cannot enter any value to this field. To modify the value in this field, first select “Graphic Editor Settings” menu option under “Settings” pulldown. Thereupon, select the “Design” tab page in “Foundations Settings” form. Enter new concrete cover value used in the design of pile caps to the “Pad Footings – Concrete Cover” field. Note that, concrete cover is measured from outer edge of the section to the center of the steel bar.
- Lx & Ly : Lx represents the length in X-axis and Ly represents the length in Y-axis for footing.
- Eccentricity X / Eccentricity Y : Eccentricity defined as the distance between center of gravity of footing in direction X or Y.

Alternatively, user may select the eccentricity of column based on the 9 given selection as show in above snapshot. Black box representing the column location. - Column Dimensions (b1 & b2) : In this field, b1 and b2 defined as the column dimension, b1 is the x-axis length and b2 is the y-axis length. The field is for preview purpose and only editable in column properties.
For non squarish or non rectangular columns, it will be converted to equivalent square or rectangle stump, based on the global plan dimensions, as shown below :
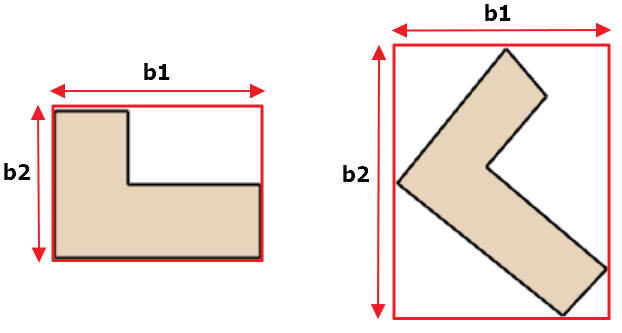
Pedestal tab (only visible for PS2025 or earlier version)

For PS2026 and later version, pedestal must be inserted in the main model first, if desired. Kindly refer to this article : RC Pedestals The Pedestal tab page comprises the pedestal and shear key dimension parameters.
- Pedestal Lx/Ly : Lx represents the length in X-axis and Ly represents the length in Y-axis for pedestal.
- Shear Key Bx/By : Lx represents the length in X-axis and Ly represents the length in Y-axis for shearkey.
Analysis Category
Materials tab
The Materials tab page displays materials settings such as concrete grade, rebar grade, diameter and soil properties for the selected footing.
- Materials (section) : This section is the same as the foundation setting in "Materials" setting
(in Building Setout tab). You may adjust the value (concrete grade, rebar size and grade) in this section and this changes apply to the selected individual pad footing only.
- Soil Unit Weight : Enter the unit weight of the fill material in this field. The volume of surcharge will be calculated and multiplied with the "Soil Unit Weight" to yield the additional axial load due to fill material.
- Soil Subgrade Coefficient : This value is only applicable when if you run FE Foundation Analysis, i.e. footing can converted to flexible raft foundation assumption. Else leave it as zero to design footing as rigid assumption.
- Fill Height : Fill height is the surcharge height. This value is automatically calculated Fill Height = Foundation Depth - Footing Depth. Value can be over-written.
- Ultimate Stress of Soil : "Ultimate Stress of Soil" will be auto-calculated by “Allowable Stress of Soil” x "Ultimate Strength Factor" value defined in the Foundation Design Setting setting found in "Center Setting" tab. Value can be over-written
Options tab
The "Options" tab page displays general setting for rebar detailing such as user defined min. rebar spacing, lean concrete thickness, increment step for depth, size and bar spacing.
- Rotation Prevented Along X/Y direction : Check this option to prevent rotation along X/Y direction.
- Show Top Rebar Outside : Check this option to show top rebar outside of the Footing.
Column Loads tab
The " Column Loads " tab page displays loading information of the selected column connected on top of this footing. User may define load combination to consider in the "User Defined" under pulldown menu.
- Loading : Choose the column loading either in Load Combination, Envelope or User Defined to design the pad footing.
- Load Combination : The footing will be designed to all the checked Load Combination.
- Envelope : The maximum value of each force, axial / moment / shear of all the combinations will be used for design.
- User Defined : Manually input forces for design
- Select / Unselect All : Select or deselect all load combination in the table.
Rebars Category
The Rebars tab page allows user to manually adjust the footing rebar design such as quantity, rebar diameter, spacing and option to bend at end bars.
When the dialog is closed using “OK” button, the footing will be inserted.
The Rebar Description are as follows :
- Rebar (X & Y) : These are bottom rebars in both direction which are auto-designed based on design moment.
- Side Bar (X-Dir & Y-Dir) : These are the side bars. They are not designed & is provided as good practice.
- Top Rebar (X-Dir & Y-Dir) : There are the top rebars in both direction. They are not designed & is provided as good practice.
- The leftmost check box is to allow user to include or exclude the rebar for the pad footing. Bottom Rebar X & Y cannot be excluded from the footing.
- User may adjust the rebar quantity, diameter, spacing and option to bend at end bar in the table (Bob).
- For example, user can manually increase the steel bar diameter or decrease the spacing if the steel is reported to be insufficient. The design is automatically re-checked if rebars are changed.
Bob stands for "Bending of Bars"
2D View & 3D View
In the pad footing properties, there are 2 tabs showing "2D Views" and "3D View".
By selecting "2D Views" , the plan view and the elevation view of footing (without rebars) will be shown with instant changes when parameter changed.
By selecting "3D View" will shows the preview of 3D footing with rebars arrangement.
When multiple vertical members are selected to insert pad footing a batch interface is opened to allow you to design all at once. You can group selected items or import a set of pad footings from CSV or Excel files. Batch reports can be prepared or design can be revised any time from the same interface.
The Pad Footing Batch Design dialog consists of top and bottom panels.
Top Panel is a row of buttons for various functionality as described below :
Design All : Allows you to design all pad footings automatically
- Option 1: Check Design (Do not redesign) - if this option is selected, the pad footing design will only be checked and no modification will be made for the existing pile cap geometry and reinforcement.
- Option 2: Check Design (Redesign if fails) - if this option is chosen, the pad footing will only be redesigned if it fails.
- Option 3: Redesign All - this option will reselect/redesign the exisitng pad footing regardless the pile cap is pass/fail.
- Design Selected : Allows to design pad footing individually by selecting single pad footing then click "Design Selected" which will brings to the individual pad footing properties.
- Group Selected : Allows to group multiple pad footings to share the same design.
- Ungroup : Allows to ungroup pad footings that grouped earlier into each individual pad footing.
- Select \ Clear All : Allows to highlight / un-highlight all pad footings.
- Reverse Selection : Allows to reverse select of pad footings. For example, total 5 pad footings (A, B, C, D, E), when A & B is highlighted, click this command, then A & B will be un-highlighted and C, D, E will be highlighted.
- Foundation Settings : Access to the general Foundation setting of the project which is same as the setting in Setting Center.
- Apply Design Combinations : Allows to select different load combinations or load envelope to design pad footing based on.
- Import From CSV : Allows user to import the pad footing(s) data from Excel (CSV format) into ProtaStructure.
- Export To Excel : Allows user to import the pad footing(s) data from ProtaStructure to Excel (CSV format).
- Detail Design Report : Allows to generate detail design report of all pad footing(s)
- OK : Click to accept the pile cap design
- Cancel : Click to discard the pile cap design
Bottom Panel is a table consists of pile cap(s) design information as described below :
Label : The label of the pad footing
Columns : The column label which is associated with the pad footing
- Load Combination : The load combination applied to design the pad footing
Depth : The depth of the pad footing
Lx : The pad footing width in X direction
Ly : The pad footing length in Y direction
Base X/Y : The base reinforcement in X and Y Directions
Top X/Y : The top reinforcement in X and Y directions
Side X/Y : The side reinforcement in X and Y directions
Design Status : the pad footing design status. If the design pass, a "tick" will be marked. Otherwise if design fails, a " red cross " will be marked.
To reopen this table dialogue, you may select multiple pad footing and select "Properties" by right click to access the shortcut menu.