Before defining a Pile Cap :
- The building model must be completed and analysed, so that the column axial loads and moments are determined.
- The foundation storey (Storey 0) must be set as the current storey.
In order to determine concrete and steel grades that will be used in the Pad Footing Design, you may go to “Building Setout” tab > Material > select “Foundation Floor” at the left hand list > select and edit concrete grade, rebar and/or soil at the right hand field.
Pile Cap Insertion

To define a new Pile Cap:
- Select and right click column(s) to access "Insert Pile Cap" at storey 0 via shortcut menu. More than one column may be selected (In this case, the Pile Cap Batch Design dialog will be launched)
- The “Pile Cap” dialog will be displayed. Check the parameters in the dialog and press the “ Design ” button to design the pile cap.
- "Number of piles" can be changed in "Pile Cap" tab if necessary.
- After completing the design of the pile cap, press the "OK” button to close the “Pile Cap” dialog and complete its insertion.
Editing an Existing Pile Cap
In order to edit an existing pile cap:
- Select an existing pile cap,
- Right-click and select " Properties " from the menu.
- Modify or auto-design of the pile cap,
- Press the "OK " button in the "Properties" form to update the pile cap.
You can repeat this process to as many members as you wish. One member at a time can be edited by this method.
Pile Cap Design Scope & Assumptions
The pile cap design module is intended for single column based on beam theory.

The pile cap module is not suitable to design a pile cap supporting multiple columns or shearwalls & core walls. For such situations, it is advisable to use the Piled Raft foundation.
The design bending moment & shear forces are based on the inverted cantilever method. Example if British Standard is selected, it would be in accordance to BS8110-1:1997 - CL3.11.2.1 and CL3.11.4.3.
For the pile cap section design, it will be categorized as either normal beam ("Shallow Beam") or “Deep Beam” based on the Reynolds Reinforced Concrete Designers Handbook 11 th Edition – Section 5.8.
This categorization is based on the ratio of cantilever span/ Effective depth.
- If the cantilever span/effective depth > 1.0 , the shallow beam method will be used.
- If 0.5 <= cantilever span/effective depth <=1.0 , the deep beam method will be used.
- If cantilever span/effective depth <0.5 , the section is too deep to be designed, i.e. no solution, and you have to either increase the pile spacing or reduce the pile cap section depth.
When you decrease the bar layers, the average effective depth of the pile cap will be increased as well. Due to this bigger effective depth, you may get cantilever span / effective depth <0.5 , i.e. no solution. If the section is categorized as “Deep beam”, the bending moment and shear will be checked according to CIRIA Guide 2 or Reynolds Reinforced Concrete Designers Handbook 10 th Edition – Table 148 based on your settings in the option. The default shall be CIRIA Guide 2.
The shape and configurations of the pile and pile caps are essentially fixed in accordance with the above stated references, based on rigid pile cap assumption (examples shown below).
Pile Cap Properties
The "Pile Cap” properties dialog will be loaded if you select a column/wall in storey 0 > right click > Click "Insert Pile cap".
The “Pile Cap” properties dialog can also be accessed after selecting an existing pile cap and then by right-clicking and choosing the “Properties” option in the shortcut menu.
There are three main categories pages in this dialog, namely “Geometry", “Analysis” and “Output”.
The “Geometry” category page comprises "Pile Cap" and "Pile Location" tabs.
The “Analysis” category page consists of "Materials", "Options" and "Column Loads" tabs.
The “Output” category page includes "Axial Loads", "Rebars", "Design Checks", "Report & Detailing", "Result " and "Optimization" tabs.
Pile Cap tab
The following information can be edited in "Pile Cap" tab:
- Pile Cap Label: You can enter the label associated with the pile cap in this field. By default, a pile cap label associated with the column label will be generated. For example, “PC-1C1” will be generated if a pile cap for column “1C1” is inserted.
- Number of Piles : You can decrease or increase the pile number by clicking and selecting the required pile number. The checks will be re-performed if this is changed.
- Depth : This is the overall depth of the pile cap.
- Shaft Type : Pile shape can be set as "Circular" or "Square"
- Penetration : Length of the pile penetrates into the pile cap (affects detailing only)
- Pile Size : Pile diameter of circular pile or pile width of the square pile
- Spacing Multiplication Factor Between Piles (Short/Long Dir): Spacing between the pile in terms of number of diameter of pile. For example, if this is set to 2.5 and the pile diameter is 1000 mm, the spacing between the piles will be 2.5 * 1000 = 2500 mm
- Distance to Face (Short/Long Dir) : Set the pile edge distance for short and long direction. A distance from the pile face to the cap edge smaller than this minimum value will not be used by the program.
- Ultimate Compression/Ultimate Tension : The ultimate compression/ tension capacity of the pile (Factored pile working load)
To check/change the pile capacity of a pile cap, user should check in pile cap properties and should not double click on the pile to open the pile properties directly. Pile Properties is for raft pile design.
- Column Type : Column shape can be set to either "Rectangular" or "Circular"
- B1/B2 : B1 and B2 are the horizontal and vertical dimensions of the column on the plan view, respectively.
Eccentricity X/Y :
- If "From Pile cap" is selected, the eccentricity of the pile cap with respect to the column in X or Y direction can be edited.
- If "From Column" is selected, the eccentricity of the column with respect to the pile cap in X or Y direction can be edited.
- Center button: To move the pile cap to the center of the column
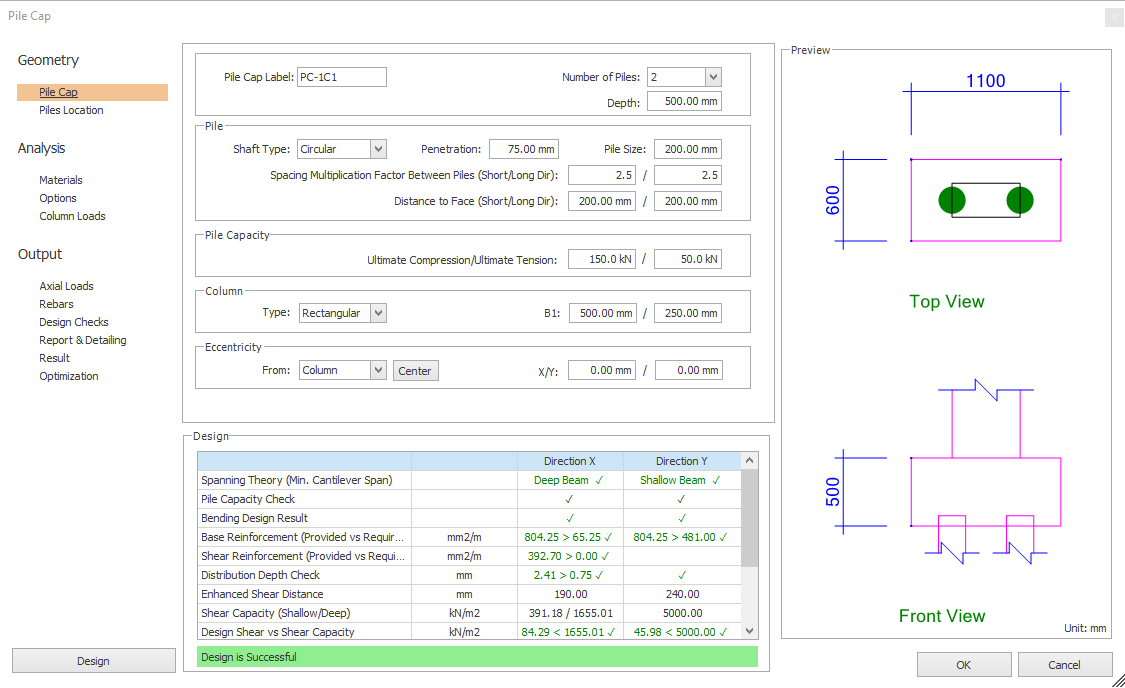
Pile Location tab
- The auto-calculated pile coordinates in X and Y directions are shown in this tab.
- The offsets of pile in X and Y directions can be edited in this tab.
- The actual coordinates of piles in X and Y directions will be calculated automatically.
- If the pile is selected in the table, the selected pile will be highlighted as "BLUE" in the Pile Cap details on the right hand side.
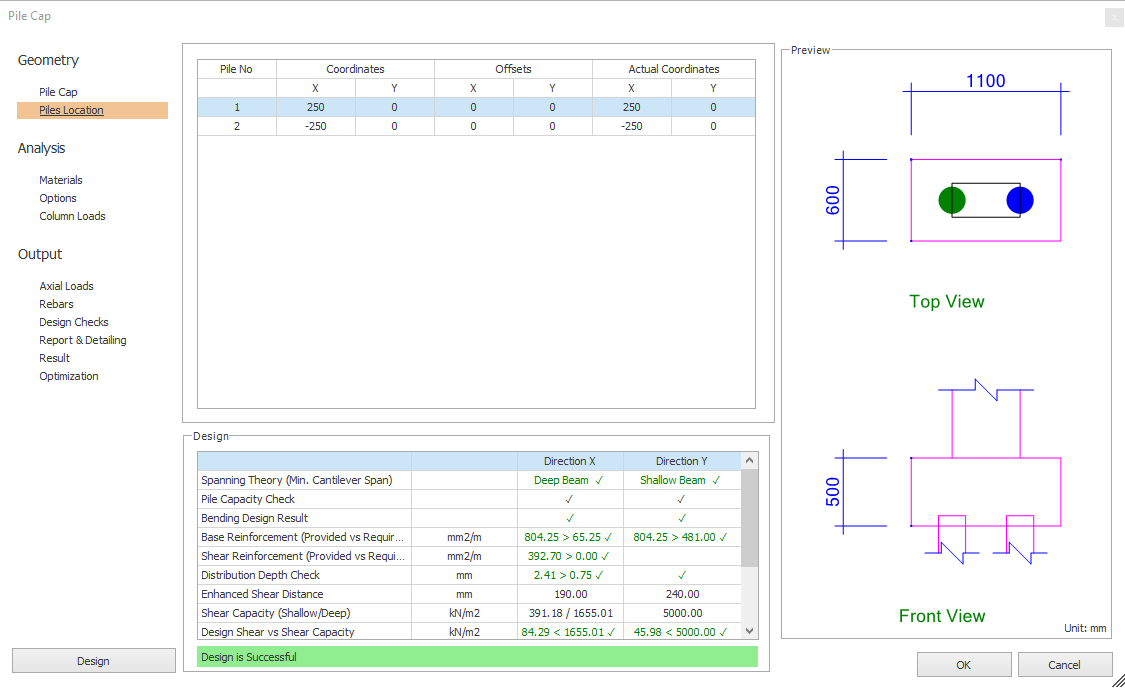
Pile offsets are meant to be small to take into account site piling in accuracies. The offsets are not meant to change the pile position and shape drastically. If the piles configuration differ significantly, then it will be more appropriate to use the Piled Raft Foundation method.
Materials tab
The concrete and rebars materials can be edits in this tab. The unit cost of the concrete, rebars, and pile can be entered in this tab if "Optimization" calculation is required in the "Optimization" tab.
The setting will be following the general setting (master setting) by default.
Concrete Material : grade of concrete for pile cap.
Concrete Type : Option to choose normal weight or light weight concrete.
Concrete Type : Surface finishes such as "As Cast", "Brushed" or "Washed".
Rebar Material : Rebar size and grade.
Link Material : Link rebar size and grade.
Unit Cost : unit cost to be calculated in "Optimization" tab.
Soil Properties : Soil weight above the pile cap will result in additional gravity load on the pile cap & higher pile forces :
- Soil Unit Weight : Enter the unit weight of the fill material in this field.
- Fill Height : Fill height is the surcharge height. This value is automatically calculated Fill Height = Foundation Depth minus Footing Depth.
- Tick User Defined to manually input fill height. V
- The volume of surcharge will be calculated and multiplied with the "Soil Unit Weight" to yield the additional axial load due to fill material.
Options tab
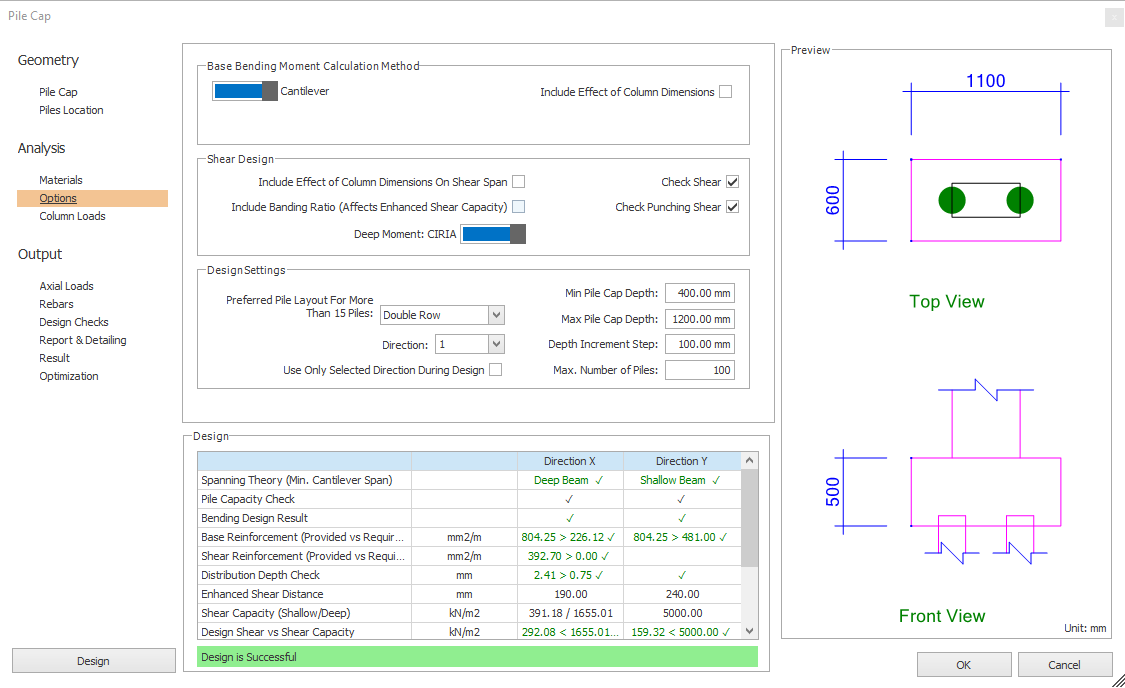
Column Load tab
The column design axial, shear forces and bending moments can be reviewed or edited in this tab
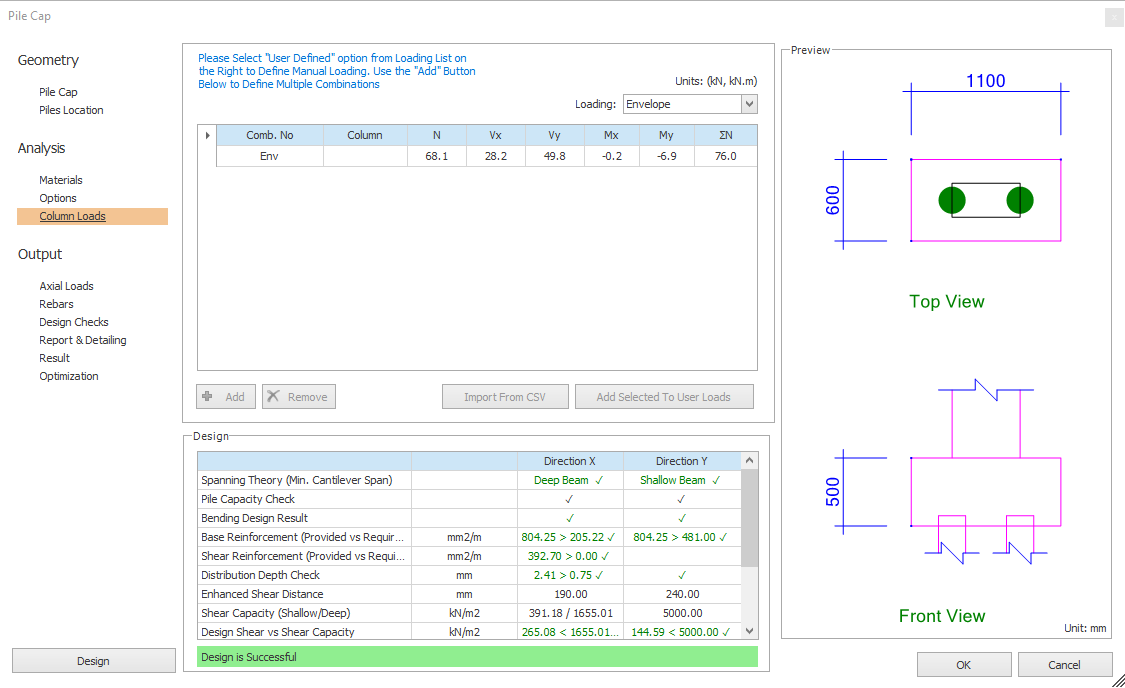
Axial Loads tab
Design pile axial forces of each piles (due to the axial load, moment and shear from the column/wall) can be reviewed in this tab.
Moment & shear of column stump will result in higher pile axial force as the shear & moment will be converted to additional axial pile forces from equilibrium equations:
- If you would like to release the moments, one option is to hinge the bottom of the column stump, i.e. hinge bottom of ST01 column.
- Shear forces in columns are inherent result of lateral forces, such as notional, wind or seismic loads. These cannot be forcefully removed from the building analysis.
The total pile design axial forces are reported in the last column. If the pile design axial force is less than or equal to the pile (ultimate) compression and tension capacities (as defined in "Pile Cap" tab), the texts in the last column will be shown in "GREEN" indicating the pile is adequate in terms of axial capacity. If the pile axial capacity is inadequate, the last column will be marked in "RED".
All values in the table (except the pile number in the first column and the total in the last column) can be edited if necessary. Then, the total pile design axial force will be recalculated automatically.
Re-calculate Axial Loads button is used for resetting all user defined values in the table and recalculating the pile axial loads.
Rebars Tab
The auto-designed reinforcement can be reviewed in this tab in a table format, including the values of As provided and required.
The description of the rebar table are as follows :
- Base (X & Y) : These are bottom rebars in both direction which are auto-designed based on design moment.
- The area of steel provided (As-prov) & required (As-Req) are shown.
- Side (X & Y) : These are the side bars. They are not designed & is provided as good detailing practice.
- Top (X & Y) : There are the top rebars in both direction. They are not designed & is provided as good detailing practice.
- This field is only active if option Use Top Bars is checked.
- User may adjust the rebar diameter & spacing.
- For example, user can manually increase the steel bar diameter or decrease the spacing if the steel is reported to be insufficient. The design is automatically re-checked, if ENTER is pressed or other cells are clicked after the change.
Rebar Options :
- Auto-select Reinforcement : Allows you to auto re-design & reselect the pile cap reinforcement. This is recommended after manually adjusting other parameters of the pile, example pile cap depth.
- Use Top Bars : If checked, this rebar will be shown in the rebar table & included in the detailing (no design).
- Use Shear Reinforcement : If checked, this rebar will be shown in the rebar table & included in the detailing (no design).
- Number of Layers (X/Y) : Specifies the number of layers of base / bottom rebar.
- By default, the auto design will only provide 1 layer.
- Manually increasing the number of layers more than 1 will increase the total provided base steel & improves the design checks that depends on this rebar.
- Generally, for Deep Beam method, the pile cap may require more than one layer of base reinforcement to satisfy the Distribution Depth Check in the Design Checks tab.
- Layer Spacing (X/Y) : Specifies the spacing of rebars between bottom steel layers if number of layer is more than 1.
- Internal Bending Radius : Specifies the internal bending radius of base reinforcement.
- This directly affects the Maximum Bearing Stress check in the Design Checks tab.
- Increasing the bending radius will improve the Maximum Bearing Stress check.
Concrete Cover : Top, bottom and side concrete covers are shown & can be edited.
Design Checks tab & Guidance on Manual Design
The pile cap auto-design will automatically design the pile cap shape, size, depth and the number of piles.
However, the design is complex with many inter-related variables. Hence, when pile caps are indicated as failed, manually amending the pile cap parameters may be necessary to achieve a pass status.
These are all the design checks, explanation & guidance on manual design, if necessary :

In performing manual design, if adjusting many of the above parameters does not work, try one or combination of the following :
- In Options tab, try changing the design parameters. For example, checking "Include Effect of Column Dimensions" generally improves moment & shear checks.
- In Pile Cap tab, try increasing the number of piles. This will generally improve many of the design checks since each pile force is reduced.
- In Pile Cap tab, try increasing the pile capacity so that less number of piles & a smaller pile cap is required.
- In Materials tab, try increasing the Concrete grade, which generally increase all capacities.
Report can be created by clicking the Create Report button in this tab
The following options can be checked if necessary:
- Add column effects to reports for all combinations
- Add pile axial loads for critical combination to report
- Add pile coordinates table to report
- Show Only critical combination results/ Show All combination results
Results Tab
If "Design" button is clicked on the left bottom of the "Pile cap" dialog, the processes will be added to this result tab. You can review the processes in the result tab if necessary. Alternatively, you can also check the final design values and checks in the "Design Checks" tab OR the "Design" table (at the middle bottom of "Pile cap" dialog)
Optimization tab
This tab allows you to perform cost analysis/optimization by listing additional candidates for the pile cap.
It will increasing the pile cap depth or pile number. Then, the total cost of different candidates will be calculated automatically for comparison.
The min. pile cap depth, depth increment step and max. number of piles can be set in the Options tab. The unit rates of concrete, rebars and pile can be edited in Materials tab.
Show Graphic toggle button allows you to switch between the table to chart view or chart to table view
Max. # Of optimization candidates : Enter the number of candidates to be generated.
List Candidates button: If this is clicked, it will generate different candidates for the pile cap
If you would like to adopt a case of the listed candidates, please double-click the row of the pile cap in the table. Then, the pile cap geometry and calculations will be updated accordingly.
Pile Cap Batch Design
If multiple columns are selected > Right click > Click "Insert Pile Cap", Pile Cap Batch Design dialog will be launched for designing the pile cap in batch mode.
By default, all select columns will be associated to a row of pile cap in the Pile Cap Batch Design dialog.
The Pile Cap Batch Design dialog consists of top and bottom panels: